Posted on: 11th January 2019 by Prof. Geoff Scamans
In my last blog, I talked about the importance of manufacturing electric vehicles from materials with low embodied carbon. As far as aluminium vehicles are concerned, we need a reliable source of end-of-life aluminium scrap in order to achieve a low-carbon recycled aluminium product. The exciting news is that, through old rolled scrap and Zorba, we have the potential to generate our own end-of-life scrap stream here in the UK.
UK demand for automotive body sheet
Estimates suggest that there is of the order of 600kt of old rolled scrap available in the UK each year, although a lot of this is actually old extruded scrap. The price of this is about 70% of the LME price for primary aluminium. This would provide on its own more than enough aluminium automotive body sheet for the present UK demand for vehicle manufacture. However, there must be the necessary automated sensing and sorting infrastructure in place (please see my previous blog) in the UK for this to be viable. You can see the details of one such UK facility here.
An opportunity from China
The UK has been exporting large quantities of aluminium scrap to countries like China and India. However, China’s import restriction on scrap has changed the situation. We should see this as an opportunity rather than a problem for UK scrap export. It could provide the incentive to utilise end-of-life aluminium scrap in the UK rather than exporting such a valuable resource.
China’s more restrictive scrap import policy has the potential to invigorate domestic recycling. It could also promote the investment in appropriate sensing and sorting technologies to provide suitable compositions for the direct manufacture of low carbon based products for lightweight vehicle manufacture.
Zorba as a scrap stream
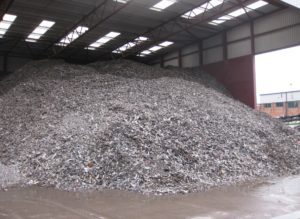
Zorba comes from shredded end-of-life vehicles and white goods and contains both wrought and cast aluminium products. The wrought alloy content can be as high as 60% depending on the mix fed into the shredder.
Estimates suggest that there is at least 250kt of this scrap stream available in the UK each year. Furthermore, it has a selling price set at about 60% of the LME price.
What is Zorba?
Zorba, as well as being a famous Greek literary character, is the collective term for shredded and pre-treated non-ferrous scrap metals. The Institute of Scrap Recycling Industries (ISRI) in the U.S. define Zorba as a ‘shredded mixed non-ferrous metals consisting primarily of aluminium generated by eddy-current separator or other segregation techniques’. Zorba is mainly aluminium but may also contain copper, nickel, stainless steel, tin, zinc, lead and magnesium. You can read more about it in an article published by Waste Management World here.
Where did the name come from?
ISRI gives an interesting explanation in their ‘2018 Recycling Industry Yearbook’. You can read it below:
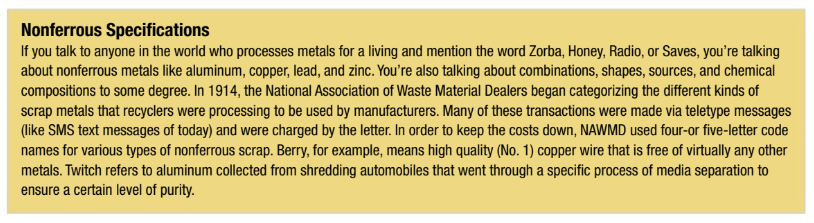
Sorting Zorba
Zorba comes in three size fractions; large, small and fine. The market has evolved to treat each grade differently. It prefers the large fraction because it is the easiest to sort using sizing equipment and dense media sorting, or by hand sorting in China. It is still possible to sort the small fraction by hand, particularly for the higher value metals in the mix. These can include copper, brass and traces of precious metals.
The fine fraction is not suitable for hand sorting. Dense media separation plants typically sort this fraction. However, they will progressively switch to sensing and sorting technologies based on x-ray transmission (XRT). Sources tell me that two of the three plants of this type in the UK have already made the switch to XRT from dense media separation.
Sorting Zorba into wrought and cast aluminium alloys using XRT is already possible. The rates are high at 30 tonnes/hour using conveyor belts that are 2.4 metres wide. A rapidly developing technology is LIBS (Laser Induced Breakdown Spectroscopy). This separates wrought alloys into AA6xxx and AA5xxx families. However, the highest rates presently available are of the order of 3 tonnes/hour. To date, sorting prompt rather than end-of-life aluminium scrap is the main use for LIBS separation technology.
The future
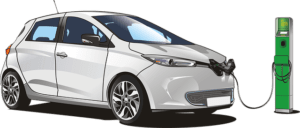
Here in the UK we must make the necessary investment in the appropriate sensing and sorting technologies. We could then establish a local source of end-of-life wrought and cast recycled aluminium to support UK manufacturing of vehicle structures.
This would be especially important for the anticipated high volumes of electric vehicles where the embodied carbon in the body construction materials becomes the critical consideration. Aluminium made from post-consumer scrap could have an embodied carbon content of less than 0.5 tonnes CO2e/tonne Al.
After all, if the drive towards battery-power is to reduce carbon emissions from vehicles, building the vehicles themselves from materials that produce high amounts of CO2 during their manufacture seems entirely wrong.