Posted on: 3rd October 2023 by Vicente Martin
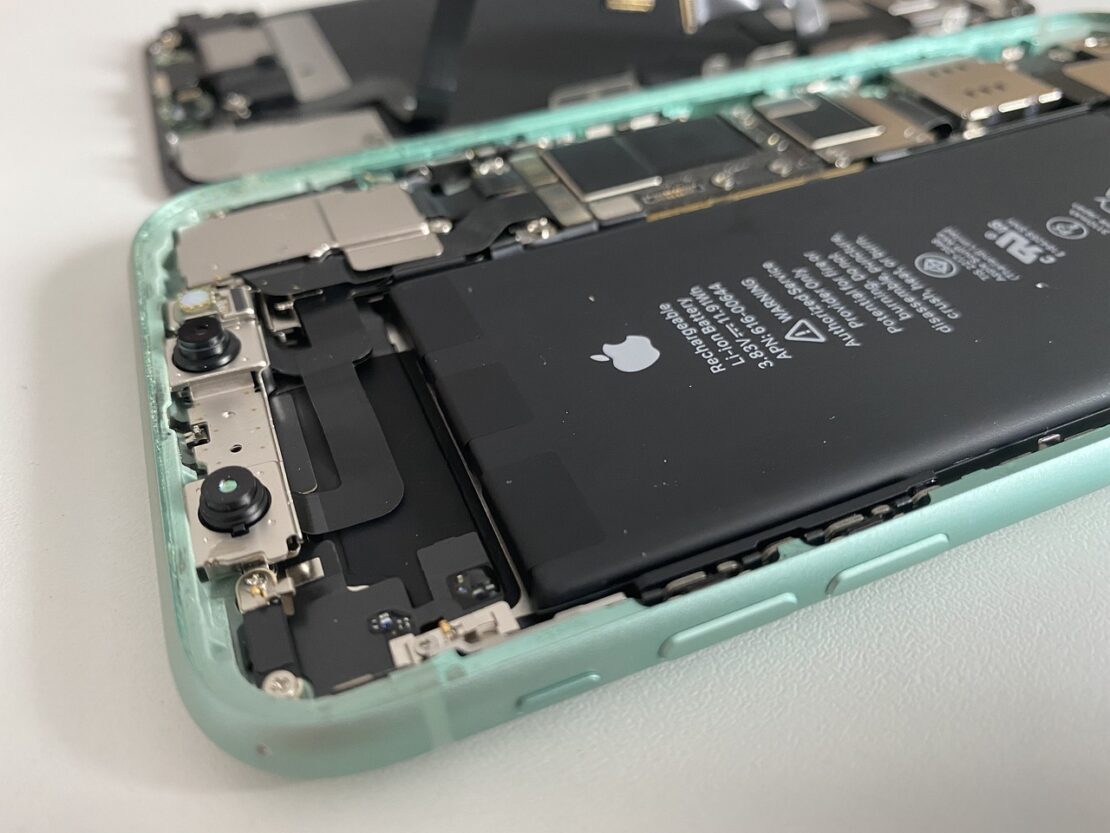
There has been considerable interest within the aluminium foil world over the past 2-3 years in so-called ‘aluminium battery foil’ as a potentially new high-volume growth market. In reality, this is a product that has been manufactured for several decades now. You’ll find aluminium foil in the batteries of cell phones, laptops and small electronic devices.
Production to date has been mainly in the Far East, with China’s interest in battery foil starting back in the mid 2010’s. However, the recent explosion of electric vehicles has fuelled the interest of foil rollers worldwide.
Although there are frequent announcements of new battery factories, only those making cells are interesting as potential customers to the foil plants.
What counts as aluminium battery foil?
There are two possible products under the global description of aluminium battery foil. The outer casing of pouch cells is a laminate very similar to a cold form foil product. It is O temper and around 40-50 µm in thickness. What we normally refer to as ‘battery foil’ is the electrode, current collector, conductor and substrate for the battery cathode. In general, depending on the application, this is an H19 product. It is 12 to 30 µm in thickness, although downgauging efforts keep reducing the thickness. It can be either single or pack rolled.
Pouch cells use a foil laminate that’s similar to some pharmaceutical foils to form the outer case. In addition to this, there are other battery components which use aluminium, including the outer casing of prismatic batteries (which resemble cans). Also, there are the interconnecting tabs or busbars connecting cells and modules. These components are thicker and in the realm of thin cold mills. However, you frequently find these products incorrectly grouped with battery foil when estimating global requirements for battery foil production.
How it’s different from other thin foils.
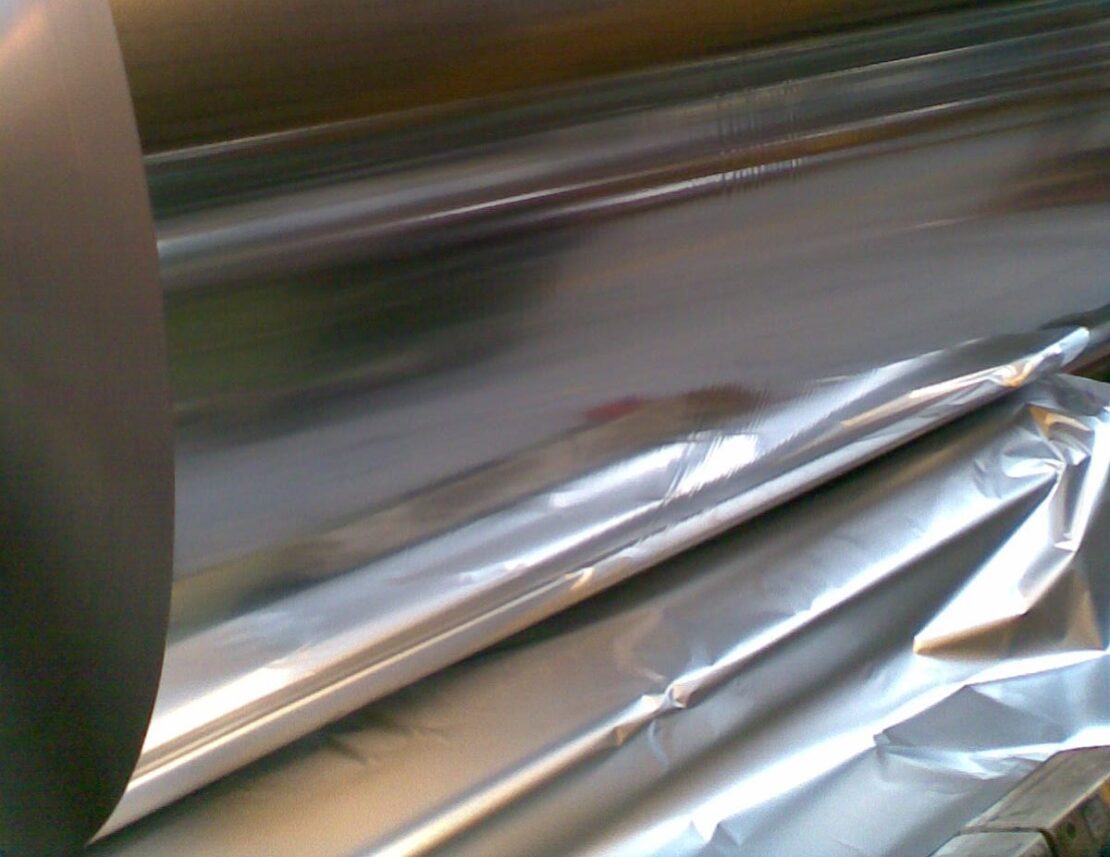
Battery foil (electrode, conductor, etc.) can be a scary novelty to thin foil plants making packaging foil.
As I’ve mentioned above, unlike most foils except blister foil, aluminium battery foil is H19 temper. This means that its surface is covered in residual oil carryover from the foil mill. The residual oil has an influence on the surface’s performance when it is in contact with the active materials in a battery. Furthermore, the foil is very prone to recovery and recrystallisation phenomena when it gets to relatively low temperatures.
Again, unlike almost every other thin foil product, producers should preferentially roll aluminium battery foil as a single strip. Unfortunately, this limits the productivity of the mill in the finishing pass. Another unusual feature is that it has a demanding combination of strength and elongation that is very important to the customer. The producer must achieve the correct combination of properties through very precise control of certain chemistries and process routes.
The specification problem.
To complicate the situation, there is a lack of standardisation and commonality in the battery industry. Consequently, there is a proliferation of specifications and requirements. It’s as though every cell manufacturer is in an arms race for performance and the continuous development of new products. In many cases, the specifications presented to the roller reflect a wish list of preferred performances, rather than an established product.
What we can do to help.
Innoval has been working in the development of industrial processes for battery foil for the past decade. We’ve gained considerable experience in the requirements of composition and process to achieve different combinations of mechanical properties, thermal stability, conductivity and surface properties.
Our knowledge helps ensure a trouble-free entry to market for new players. For those already making foil, we can speed up the development of foils with exciting new properties.
If you’d like to explore how we can support your aluminium battery foil project, please contact us.