Posted on: 7th November 2022 by Dr. Junjie Wang
Have you ever used aluminium household or kitchen foil? If so, you have probably noticed that one side is more shiny or brighter than the other. Not many people think about why there is such a difference. Even fewer people know it is related to the surface finish and roughness of the foil.
Aluminium foil products are produced by flat rolling (in one of our previous articles you can read a brief history of metal rolling). The thickness of household foil is typically only 10 to 16 µm. However, some heavy-duty household foil can be up to 25 µm. In the production of foil products thinner than 25 µm, the final step is usually ‘pack rolling’ two layers of foil at the same time on a doubling mill. As such, one side (the bright side) of the foil is in contact with the steel roll while the other side (the matt side) is in contact with the other foil. The two foil layers are then separated after the pack rolling process.
As you can see in Figure 1, the bright side of the foil shows directional rolling marks which come from the roll surface. This side usually has a lower surface roughness (depending on the roll surface roughness). It reflects light mainly in a specular way which makes it look bright. The matt side has a higher surface roughness but is less directional in surface finish. This makes it reflect light more diffusely than the bright side.
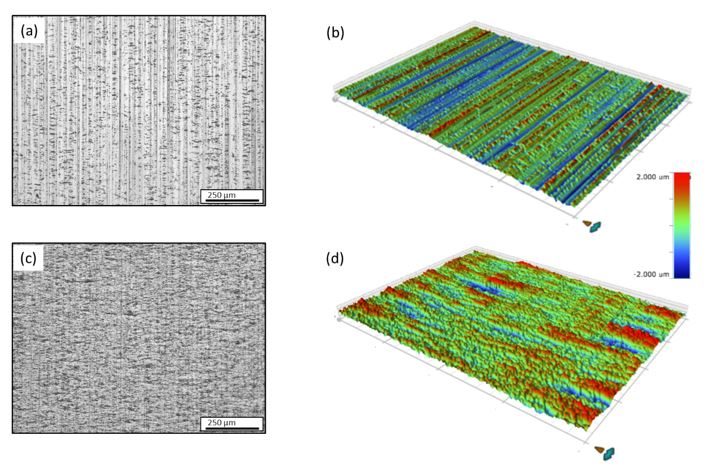
In this Insights article, I am going to give some more examples of why surface finish and roughness is important to many aluminium products, and how to evaluate it.
Why is surface finish and roughness important?
1. It provides a certain visual appearance and touch feeling.
Not many people care much about the visual appearance of household foil as long as it looks clean. However, many people take the appearance and the touch feeling into account when they buy mobile phones and laptops, etc. Technically, they are selecting the surface finish and roughness of the metal enclosure.
2. It holds a certain level of rolling lubricant during processing.
While this can be helpful during the manufacturing process, it can also affect how the material performs in service. For example, aluminium foils are now extensively used as electrodes in batteries. For this application, the surface conductivity and wettability of the foil is extremely important. We do not want the foil surface to hold too much lubricant as it passes through the foil rolling mill. Therefore, a small surface roughness value of the order of a tenth of a micron is usually preferable.
3. It affects friction between the workpiece and tools during forming.
This is a vital consideration for many industry sectors where the aluminium material is required to undergo forming operations to produce a finished component. In the automotive industry, for example, there are two surface finish types for aluminium sheet panels; mill finish (MF) and electro discharge texture (EDT). Figure 2 shows examples of both.
Mill finish surface is characterised by unidirectional grit lines. It is the standard output from a cold mill and reflects the roll grinding practice. Electro-discharge texturing (EDT) produces a well-controlled texture (built up from microscopic craters) on the roll barrel surface. This pattern transfers to the sheet surface during a final light reduction pass (up to 5% reduction) at the end of cold rolling. German Automotive Association specification VDA 239-200 requires an EDT surface to have an average roughness (Ra) of 0.7 – 1.3 μm. For mill finished surfaces in the transverse direction, it is 0.3 – 0.6 μm.
The valleys on a mill finish surface and the pockets on an EDT surface help to hold lubricant. This is essential for forming the sheet into shapes. Adequate transfer of the topography during the final texturing pass, with the right surface quality, is a key challenge for mills producing automotive sheet.
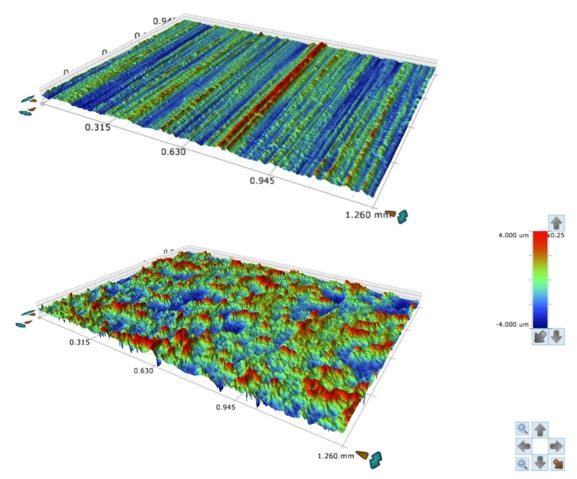
In beverage can production, if the surface roughness of the can body sheet is too high, it increases the friction between the aluminium and the tool during the deep drawing process. This may result in a higher level of galling and even breakup of cans.
4. It impacts the bonding of aluminium and adhesives or paint coatings.
A rough surface gives additional surface area for the adhesive or paint to stick to and form a bond. It also provides sites for mechanical interlocking at the interface. However, excessive surface roughness may not be a benefit. The overall contact area might decrease, and air could be trapped at the interface, depending on the viscosity of the adhesive and paint. Some parts of the coating industry have been investigating a laser ablation process, which modifies the roughness of the aluminium surface, as a pretreatment for adhesive bonding.
5. It affects fatigue strength.
The fatigue life of a component decreases with increasing surface roughness, especially in high cycle fatigue. With respect to the direction of surface roughness, the fatigue strength is more strongly influenced by circumferential direction roughness normal to the stress direction than in the axial direction. When evaluating the fatigue life of aluminium products during service, or designing high fatigue life aluminium components, you must take the surface roughness into consideration.
Analysing surface finish and measuring surface roughness.
Historically, surface roughness has tended to be measured using a mechanical contact profilometer in which the sample surface moves relative to the stylus of the profilometer. Nowadays, we use optical methods such as interferometry and confocal microscopy as they are simple, quick and economical. These optical methods can measure the surface topography within a single camera acquisition, typically between a few seconds and 10 minutes.
We can export all kinds of data such as contour maps, line profiles at selected positions, and analytical results. The contour map in Figure 3 clearly shows Type A Lüders lines (horizontal lines in the figure) on a AA5182 automotive sheet surface. The corresponding Y profile shows the magnitude of the waviness caused by the presence of the Type A Lüders lines.
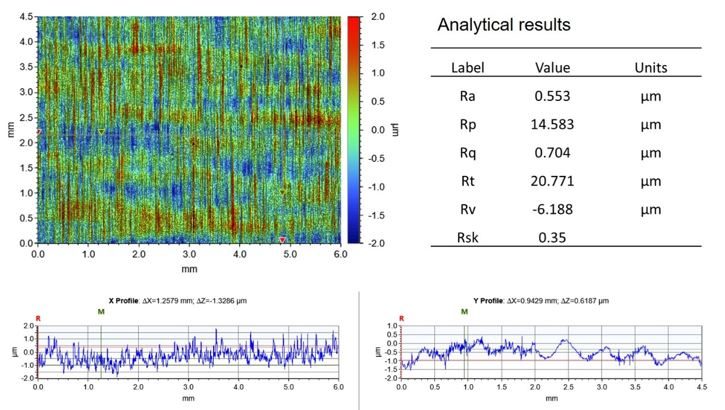
Contact and pseudo-contact methods such as atomic force microscopy (AFM) and scanning tunnelling microscopy (STM) can be used for high resolution surface roughness analysis at the atomic level. This means it is possible to obtain resolutions of the order of fractions of a nanometre. However, the speed of measurement is much slower than that of optical methods.
Support to control your product surface.
As you can now see, the surface roughness of aluminium rolled products is a result of many parameters including roll grinding, lubrication and rolling operations, downstream forming processes etc. Here at Innoval we have a huge amount of expertise in this area. We work with our clients to control and improve the surface finish / surface roughness of their products to meet and exceed the market requirements. If you are interested in how we can help you optimise your product surface, please get in touch.