Posted on: 25th August 2016 by Kyle Smith
Recently we’ve posted a series of blogs which illustrate the practical application of our aluminium rolling process models.
We’ve shown how our rolling model can help determine work roll camber. We’ve also shown how our strip quench model can lead to an increase in productivity. Now it’s the turn of our tension leveller model for strip levelling.
Strip levelling with a Tension Leveller
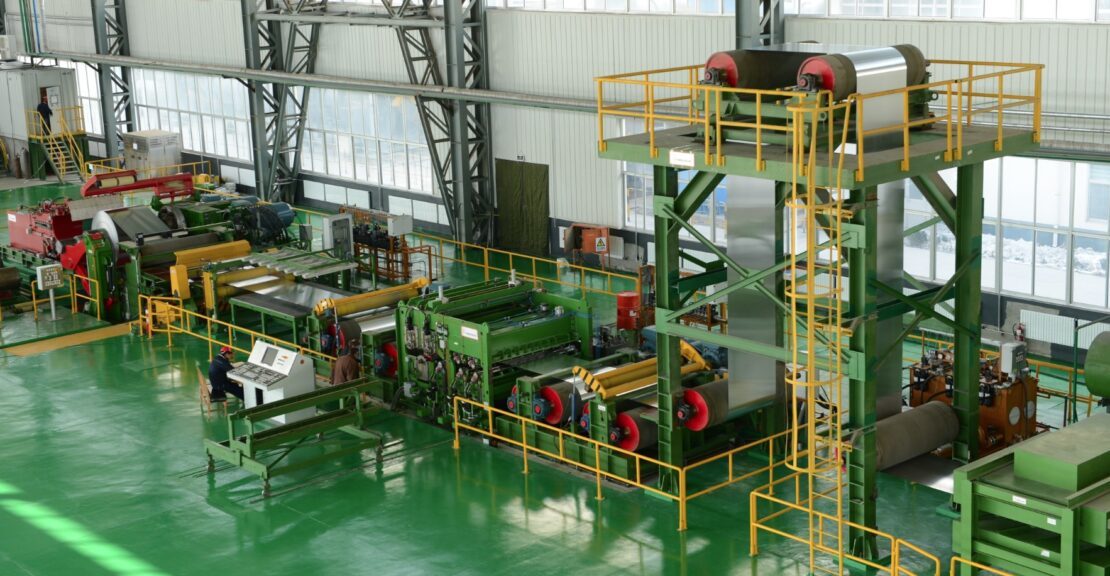
Tension levellers correct some of the off-flatness caused by the rolling process. You can read a brief description about how they work here.
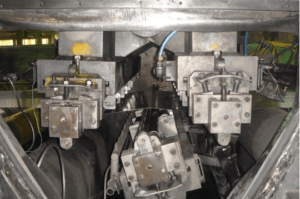
Rolling mills may contain flatness control systems to help the operators minimise strip off-flatness defects from the rolling process. However, some strip levelling is usually required to produce the extremely flat strip that some customers now demand. This is especially the case if the strip flatness has changed within the rolled coil as a consequence of the coiling tension and strip profile (variation of thickness across the width).
Our tension leveller model calculates the stresses and strains in the strip as it goes round the rolls in a tension leveller. In this blog I’m going to explain how the roll geometry can be set up and the model run to predict strip elongation.
Strip elongation
Strip off-flatness occurs when some regions of the strip across the width are shorter (or longer) in length, in the rolling direction, than other regions. If these length differences are sufficiently large then the off-flatness can manifest as visible buckling of the strip. The loose regions are simply longer than the tight regions.
The level of off-flatness and buckling can be reduced by extending the strip sufficiently in the rolling direction such that it is permanently (plastically) deformed and the remaining strip length differences are small. This is the strip elongation. Lengthening the strip in this way reduces the off-flatness and removes the buckle. This is what the tension leveller does.
Below is a simple geometry that can be a small part of a much larger levelling machine. The strip enters from the left and passes over and under three rolls. As the rolls turn, the leveller controls the tension between each pair of rolls.
The rolls tab shows the fully editable table of roll names, x position, y position, radius, rotation (clockwise or anticlockwise) and the tension after each roll.
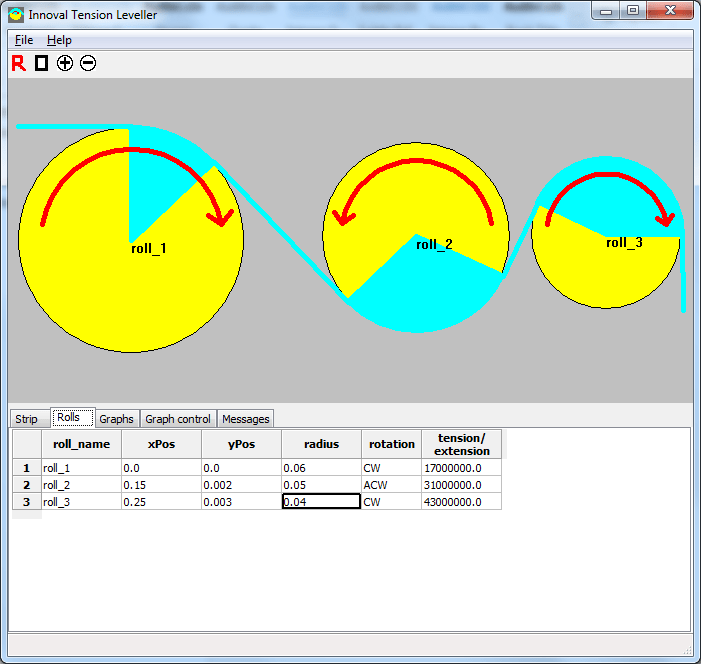
Increasing the strip elongation
When the model is run, the ‘Messages’ tab summarises the model’s predictions. In this example, we can see that the plastic strain of the strip leaving the third roll is 563 microstrain (0.000563 strain).
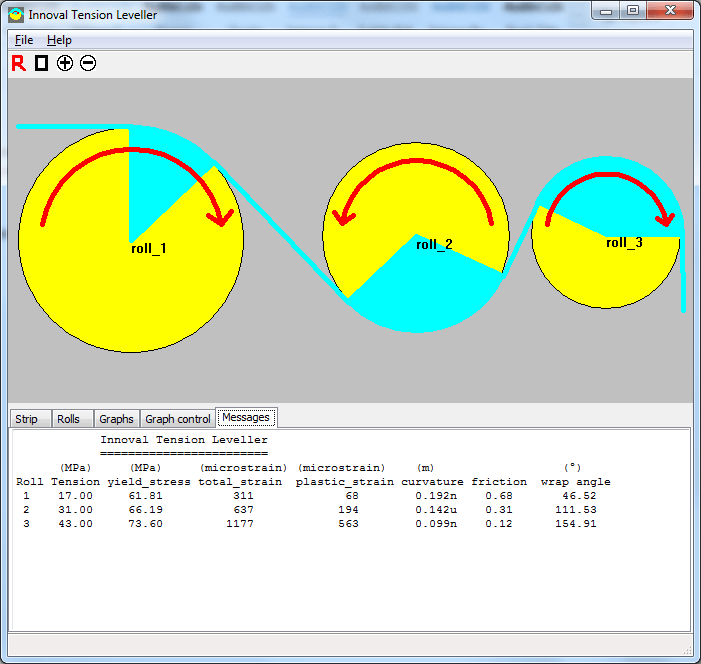
If this is not enough elongation, there are many ways of increasing it. However, two options are as follows:
- reduce the roll diameter of the third roll
- increase the exit tension of the strip coming off roll 3
Let’s take the first of these options and reduce the radius of roll 3. If we change it to 0.02 m and run the program, the plastic strain increases to 968 microstrain.
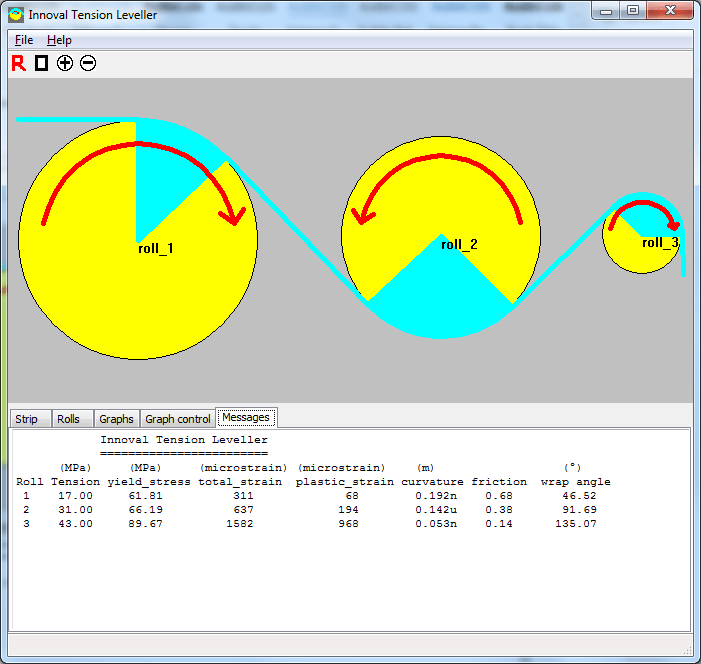
Now let’s look at the second case. If we increase the tension of the strip coming off roll 3 to 50 MPa, the plastic strain increases to 1084 microstrain.

Clearly, these are not the only strategies we can employ to control elongation. We can manipulate the other two roll radii and tensions to influence the elongation. However, this serves as an example as to how the model helps to determine the leveller set-up. Consequently, we can optimise strip levelling without disrupting production.
Aluminium rolling process models
A fast running model such as this one is useful in teaching the basics of strip levelling. Furthermore, it’s a great way to optimise your processes without interrupting production.
Our tension leveller model is part of a suit of models we’ve developed for the aluminium rolling industry. You can find out about them here. We use our models as tools in our consulting business. However, you can also buy all our process models to use yourselves under a license agreement.
This blog post was originally written by Dr Rade Ognjanovic who has now left the company. Please contact Kyle Smith if you have any questions.