Posted on: 30th September 2016 by Kyle Smith
As part of our series of blogs about aluminium rolling models, I’m going to talk about roll cooling and the Innoval Spray Impact Model (ISIM).
I’ll describe some of the common problems we encounter when working with spray systems on cold rolling mills, and how ISIM helps us to solve them.
ISIM is one of our most frequently used models. It is a precision tool for modelling the effectiveness of rolling mill spray cooling systems. You can use it to accurately evaluate your current equipment set-up. Or you can use it to design new spray headers which meet the challenges of modern rolling mills.
>100 roll cooling studies
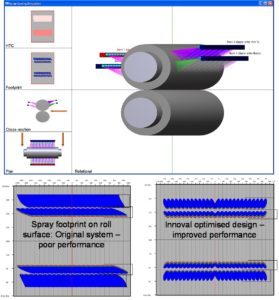
At the heart of ISIM is the experience and knowledge of Innoval’s experts. They’ve spent years working in the aluminium rolling industry.
Between them, our staff have carried out over 100 roll cooling studies. As such, they’ve improved the performance of many rolling mills around the world. They’ve also been able to extensively verify the model.
ISIM’s deep physical description of roll thermodynamics and cooling spray heat transfer, as well as its comprehensive inputs, mean it can confidently model any situation.
Level vs pulsed control systems
It is often the case that older spray cooling systems operate using level control, usually with seven levels. Three spray bars with nozzle flow rates in the ratio 1-2-4 achieve this. Switching on only the smallest flow rate nozzles gets you the lowest level. The highest level comes from switching on all of the spray bars at once. The levels in between can then be obtained by using various combinations of rows on spray bars.
One major issue with most level control systems is that, whilst the flow rates are in a fixed ratio, the cooling effects of each spray bar are not as neatly proportioned. This is because the cooling effect of each spray bar is determined by a host of other factors in addition to flow rate. These include the size of the spray footprint on the roll surface and the angle of impact with the roll surface. Layer cooling and the interactions with neighbouring spray bars also play a part.
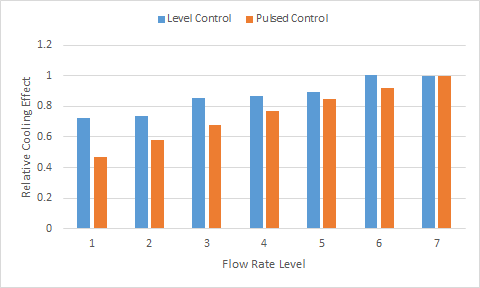
Figure 2 shows a comparison between the relative cooling effects of different flow rate levels in a level control cooling system on a cold mill. The data is taken from a real-life example.
Figure 2 also shows the predictions for a replacement pulsed control system. ISIM, along with measured roll temperature data, generated this chart. However, we also used the Innoval Rolling Model to assess the heat flows involved in a typical process.
The results show that the increase in cooling effectiveness is much smoother for pulsed systems than for level control. Also, the difference in cooling effect between levels in a 1-2-4 system can be minimal. This leads to ineffective flatness control.
Spray footprints
A second problem encountered with level control systems is that cold mill rolls are typically fairly small in size. This makes it a challenge to direct three spray bars onto the surface of a roll in an efficient manner.
If the spray footprints are too close to each other on the roll, their interactions can have a very negative impact on the overall cooling effect. In some cases, higher levels can even have a reduced cooling performance instead of the assumed increase in performance. You can see this between levels 5 and 6 in Figure 3.
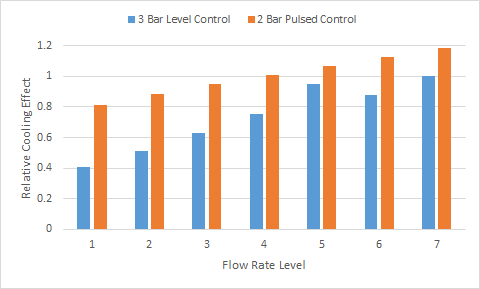
For these reasons it is often advisable to switch to a two spray bar system using pulsed control. You can size these bars to achieve the same maximum flow rate, but apply the coolant in a much more efficient manner. This is because they can be more spaced out than the three spray bars required for a 1-2-4 level control system. On small cold mill rolls this usually leads to a significant improvement in cooling effect, allowing for increased speeds and productivity.
Figure 3 shows results generated using ISIM which compare the relative cooling effects of a three bar level control system and a two bar pulsed system. Each level uses the same coolant flow rate.
Optimisation studies
Insightful findings such as these mean that we are world leaders in roll cooling spray bar design. Because of this, spray system manufacturers come to us for our modelling capabilities when designing new systems.
Our Process Improvement team uses ISIM to design systems with excellent profile control in hot rolling. They also use it to design systems with exceptional flatness control in cold rolling.
We frequently employ ISIM to tell clients how their current cooling system is performing. What’s more, we then show them what they need to do to improve it. If you’d like to discuss this further, please get in touch.
Finally, please have a look at this animation of ISIM for more information.
This post was originally written by Dr Timothy Clemson who has now left the company. Please contact Kyle Smith if you have any questions.