Posted on: 17th February 2016 by Prof. Geoff Scamans
It’s crucial that Innoval remains at the forefront of developments in the aluminium industry so that our clients can be confident that our technical knowledge is as up to date as it can be. One of the ways we do this is by being involved, as leaders or partners, in UK-Government funded (via Innovate UK) collaborative R&D projects. We’ve been involved in 20 such projects over the last 10 years and this has strengthened our interactions with both the UK Science base and the OEMs.
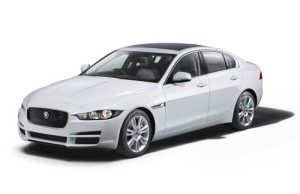
One of these projects, REALCAR (REcycled ALuminium CAR), has received a lot of publicity recently on account of its success in catalysing the transition from steel to aluminium for Jaguar Land Rover body structures across their whole vehicle range, and we’re proud to say that we played a significant part in the initiation of this project.
The project’s success hinges around a significant breakthrough in the cost to use aluminium sheet for automotive structures. Some 10 years ago we had discussions on the imperative for lower cost aluminium sheet with Mark White, Chief Technical Specialist, Light Weight Vehicle Structures at Jaguar Land Rover (JLR). We realised that the only way to get to the JLR cost and sustainability targets was to use as much recycled aluminium as possible and to minimise the use of prime metal. The aim was to effectively treat aluminium in cars in the same way as aluminium in cans by recycling at every stage of production and at end of life. The shorthand notation for this conceived at the time was “Cans to Cars”. The outcome of these discussions was our formulation and development of the REALCAR project that was funded through a collaborative R&D competition launched by Innovate UK in 2007. The other partners in the project aside from us and JLR (as the project leader) were Novelis, Stadco, Zyomax, Norton Aluminium and Brunel University. Innovate UK contributed approximately 70% of the funding towards the £2 million project.
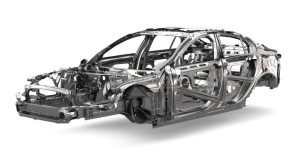
The REALCAR project demonstrated that it was perfectly possible to make the AA5754 structural sheet alloy from segregated and returned press shop scrap without any sacrifice in performance. This version of the alloy is now being promoted by JLR and Novelis as RC5754. The new Jaguar XE was the first vehicle build to use RC 5754 and future models like the 2016 XF and F-Pace SUV will also use this alloy. The concept has also been extended by Novelis for the AA6xxx automotive alloys. As JLR generate about 50% of sheet scrap during their pressing operations for vehicle body-in-white manufacture, they ensure that all this scrap is segregated by alloy family type and is directly returned to Novelis for further automotive sheet manufacture. Novelis has set up casting facilities at their Latchford recycling plant in the UK to cast rolling blocks from the returned AA5xxx and AA6xxx press shop scrap essentially as RC5754 and RC6xxx. The value of the press shop scrap is about 90 to 95% of the LME aluminium price and this effectively means that the price paid by JLR for their sheet from Novelis is discounted by a significant fraction of the LME price for every second rolled coil. This significantly reduces the cost of using aluminium sheet for vehicle construction and has made a major direct contribution to JLR’s sheet purchases worth millions of pounds.
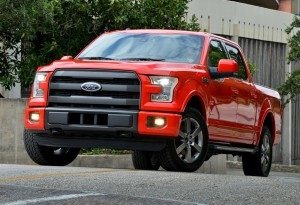
It doesn’t stop there though; Novelis has since helped Ford develop a similar closed-loop press shop scrap recycling system as that used by JLR in the UK, although with more returning scrap streams. Ford installed $60 million worth of scrap-handling equipment and now trailers full of aluminium scrap are shipped back to Novelis or Alcoa for reprocessing.
Through REALCAR, the simple “Cans to Cars” recycling idea has had major global ramifications for both the aluminium industry and major OEMs like JLR and Ford and will continue to deliver major financial benefits for many years to come. We’re proud to have instigated such a successful project which not only enabled two global OEMs to embrace vehicle lightweighting through the use of affordable aluminium sheet (which is also great for our industry), but which also has significant environmental impact.
To read about our expertise in automotive lightweighting technologies, click here.