Posted on: 27th May 2016 by Kyle Smith
A ‘model’, in the engineering sense, can mean different things to different people. You may have noticed that in our suite of process models, there is something called a Process Cost Model. This post will briefly explain how this type of model can help with many familiar process engineering issues.
With Innoval’s Process Cost Model, easily identifiable process parameters such as line speed, target temperature, residence time etc. are input by the user. The model then calculates and predicts the resulting outcomes, simulating the behavior of the real process as far as possible.
Why use a Process Cost Model?
Quite simply, the use of such models means that otherwise expensive and time-consuming trials can be carried out without any disruption to the real production lines or without jeopardizing very expensive equipment and materials; there’s a health and safety benefit too. ‘What-if’ scenarios can be safely explored and thoroughly tested in a virtual environment.
What counts as a cost?
Increasingly these days, financial costs, e.g., the costs of energy supplies, raw materials, disposal of wastes and by-products, labour etc. are always under scrutiny. In the simplest configurations, so-called ‘variable’ and ‘fixed’ costs are usually included. ‘Variable’ being the term used to encompass those costs which scale with production effort; ‘fixed’ being those that are present even at zero production.
There are other costs too; the costs of finance for example. Many companies are required to borrow money in order to fund capital equipment expenditure (CAPEX). Not only does this need to be repaid, but the interest on that loan also requires servicing.
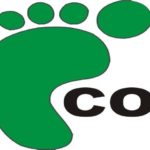
In more recent times, there are other ‘costs’ that many companies now wish to consider too. Environmental impacts are also ‘costs’. Consequently, the carbon footprint of a particular product (expressed in terms of its ‘carbon dioxide equivalent’) is often a metric that is used and reported.
The largest costs in a process sequence are not always obvious and this is where a process cost model can really help. For example, aluminium sheet is often coated with paint or lacquer for a variety of purposes. These coatings traditionally require the use of a thermal curing cycle. This means the coated metal is passed through a large oven to evaporate any solvent present, and to bring about the chemical and/or physical transformation of the coating.
It is perhaps not surprising that, given the large physical size of these curing ovens, they are often assumed to be the most expensive parts of the process. They do, after all, consume large amounts of electricity and/or natural gas. It was a matter of some consternation to a client then, when process cost modelling revealed that it was actually the cost of the paints and lacquers that were their largest cost items and by quite a long way too (Figure 2).
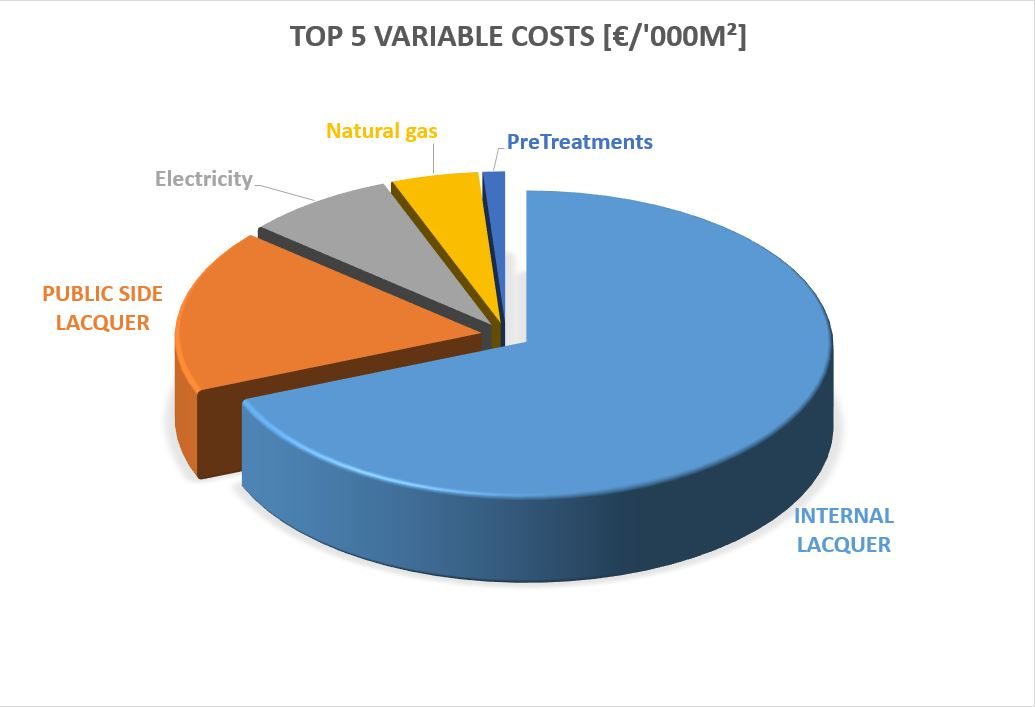
How much do I get out, for the amounts I put in?
It is often reasonably well known how efficient a particular process step is in terms of mass-in and mass-out. However, where processes are ‘closed’ (scrap or by-products are tidily removed away automatically and hidden from view), or processes are sequential (as is the case in many continuous aluminium sheet processes), identification and evaluation of discrete process recoveries can be more difficult. This is where cost models come in. They can assist in the process-by-process recovery calculations which show where significant losses are really occurring. Process improvement activities can therefore be focused on the processes which will benefit the most.
But what about the material that gets recycled?
The aluminium industry prides itself on being good at recycling. Most processes in our industry will generate aluminium metal waste or scrap. This could be large pieces such as the butt ends sawn off cast ingots or edge trim from rolled sheet, down to chippings and swarf generated when sawing or scalping. Any process model should be capable of handling this recyclate or ‘feedback’ material, and re-introduce it into the process flow scheme at a suitable point.
Processes are not always stand-alone.
As well as being able to use process cost models to evaluate process capacity, models (and combinations of models) can be used to determine not just how many, but what size the equipment needs to be to achieve the desired output. Often this type of calculation is necessary because the individual interconnected processes are themselves a complex series of sequential operations.
If you think a process cost model could be just what you need to safely and efficiently optimize your processes, please get in touch. We’ll work with you to create a model of your processes, allowing as many different parameters as you like to be adjusted and their effects investigated – without affecting real-life production.
This blog post was originally written by Andy Darby who has now left the company. Please contact Kyle Smith if you have any questions.