Posted on: 29th March 2018 by Prof. Geoff Scamans
We’ve all read recently about the scandal of plastics floating about in the rivers and oceans of the world. Of course the retail / packaging industries do themselves no favours with stories such as the cauliflower “steak” in a plastic tray covered in film. We all hate having to tear off that nasty, unnecessary packaging to get to our deliciously nutritious ready meal.
In the aluminium industry we feel righteous about the recycling record and environmental credibility of cans, don’t we? Reported recycling rates of beverage cans were 99% in Germany and Finland, and 73% in Europe in general in 2014.
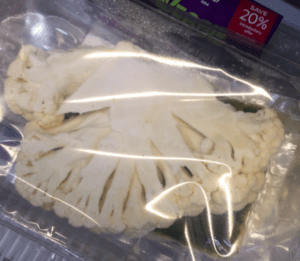
In this blog I want to sound a few cautionary notes about babies and bathwater, and why we need to think hard about becoming entangled in the clamour for the elimination of plastics.
Here I’m lumping coatings and lacquers in with plastics since they’re all polymers. They come from the same starting stock (oil), have the same stubborn resistance to degradation and ultimately will end up as carbon dioxide.
Polymer coatings on beverage cans
Let’s start with the beverage can. It’s a great success story when it comes to low carbon footprints. Boy scouts, girl guides and charity collectors the world over love them!
In 2011, in the EU, 16% of aluminium rolled products went into beverage can manufacture (1). Polymer coatings cover all internal surfaces and most of the outside of aluminium cans. If we assume a coating thickness of 1 µm (about one hundredth of the thickness of a human hair), this translates to 2500t of coating on 59 billion cans. We apply these polymer coatings to the cans largely for protection and decorative purposes.
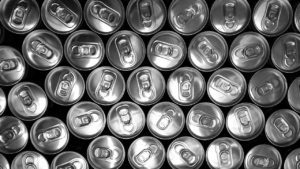
Protection works both ways: we have to stop the aluminium from interfering with the drink, and also stop the drink from eating away at the aluminium can.
The fact that this amount of coating might seem relatively small given the size of the beverage can industry is testament to the effort put in to minimise material use. This goes for the metal as well as the coating. In general packaging companies want to use as little of the Earth’s resources as possible. Put like this, they sound like a very altruistic bunch. However, it all comes down to money. Polymer coatings and aluminium cost something. Therefore, reducing the amount used, in general, reduces costs.
It’s not all bad news!
So what happens to this 2500t of polymer coatings when the cans are recycled? In a nutshell, it gets burnt off. However, do not despair. This isn’t the big, black environmental mark against can recycling that you might believe. This is because we use the energy released during can decoating to help heat up the furnaces that melt the aluminium. We need to heat and melt the aluminium to transform it from cans back into ingots, which we then use to make other useful products.
Bioplastics
I like this description of the coating being a staging post in the life cycle of oil. Unfortunately, it still ends up as carbon dioxide emissions and contributing to the Earth’s greenhouse gas problem. However, we’ve diverted its path more than if we burnt the oil, say, in a car engine. But wouldn’t it be better if we didn’t use petroleum based coatings at all? What about bioplastics? Could we make polymers, including coatings, from sustainable sources?
Well yes, it’s already done. In 2009 Coca Cola launched their Plantbottle, “the first-ever fully recyclable PET plastic bottle made partially from plants”. A couple of points I should mention here: Coke’s development is a recyclable plastic which can integrate into current PET recycling systems. Although it is a bioplastic, it is not biodegradable. Consequently, since Coke has distributed 40 billion Plantbottle packages worldwide, it is possible that some of the debris found floating in the Pacific is bioplastic.
Eliminating plastics
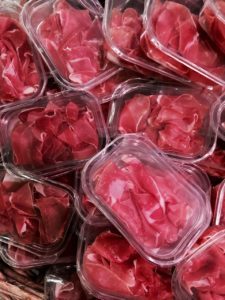
Conversely much has been made of efforts to “eliminate plastics” by substituting biodegradables, notably in one supermarket in Amsterdam (2). You might care to look at the blog of Tetracycle founder Tom Szaky (3) for a description of why you’d need an industrial composter (and not your garden heap) to break down the biodegradable polymers in use.
Another thing to consider is that bioplastics don’t grow on trees. They actually start life as crops growing in fields. At the moment the availability of fields is, as far as I understand it, limited given that we generally want to grow food without resorting to a vast increase in the use of fertilizers, pesticides etc. However, that’s a whole new blog for someone else to write.
A note of caution
To finish, I think we need to be cautious about “eliminating plastics”. They cover a wider range of useful products than the litter they are commonly portrayed as. In the aluminium industry we coat a lot of our products. It’s a simple fact that these products could not exist if we didn’t. Bioplastics may become useful when we’ve learnt how to farm them efficiently without disrupting food production. In the meantime, let’s think about how we make best use of oil based products before sending them up the chimney. Furthermore, let’s recognize that ultimately energy recovery through thermal recovery is critical.
If you need support choosing, optimising or minimising your aluminium coatings, read how we can help you here. If you have any questions, please feel free to contact us too.
References:
- 1. Joerg Sander, “Coil Coating”, p. 147 (Vincentz Network), 2014
- 2. https://www.theguardian.com/environment/2018/feb/28/worlds-first-plastic-free-aisle-opens-in-netherlands-supermarket
- 3. https://www.huffingtonpost.com/tom-szaky/bioplastics-and-the-truth_b_8954844.html
This blog post was originally written by Dr Colin Butler who has now left the company. Please contact Prof Geoff Scamans if you have any questions.