Posted on: 16th March 2018 by Private: Helen Forrest
Knowledge Management is a ‘hot topic’ for many companies at the moment, including those in the manufacturing sector.
Many operations already have systems in place to manage their tangible knowledge; that’s reports, presentations, papers etc. However, they often overlook the knowledge and experience of their people. A highly skilled and knowledgeable workforce is often a company’s most valuable and unique asset, so shouldn’t something be done something to safeguard this knowledge as well?
What if there was a way to keep all of this knowledge, tangible and tacit, together in one place? This blog briefly introduces Innoval’s approach to Knowledge Management which will do exactly this.
However, first of all, let’s consider some situations within a manufacturing environment where Knowledge Management is critical. You may find some of them familiar.
Ageing workforce or specialist
Picture your Technical Manager who has been in the industry for over 30 years. Many of these may have been spent with your company. However, he’s due to retire next year and so all that knowledge and experience will retire with him. Can you afford for that to happen?
Reinventing the wheel
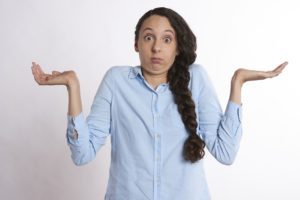
How many times have you been faced with a problem only for someone to helpfully say ‘exactly the same thing happened 5 years ago’? However, no-one’s got any record of what was done to fix the problem or why it occurred in the first place.
Now you have to go through the whole problem-solving process again. It’s frustrating, it’s a waste of time and it could have serious consequences for your business in terms of customer satisfaction.
Untapped knowledge
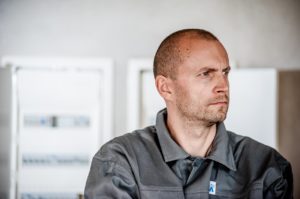
Most people appreciate that talented process operators often know most about running a process successfully.
There may even be ‘black art’ tricks that may not be in the Standard Operating Procedures, but which they need to do in order to process particularly difficult products.
Does only one shift know about this? Has anyone written any of it down? Is there a better way of running the process? There may be a rich seam of knowledge in your company that you’re just not exploiting.
Knowing the knowledge gaps
Do you know what you don’t know? This is a question we rarely ask ourselves. However, once you know where your knowledge gaps are, you can work on filling them to gain competitive advantage.
On a practical note, if you manage your knowledge effectively it makes using it simple and easy. Furthermore, having it all available in one place makes training more efficient.
A practical solution to Knowledge Management
Hopefully, by now you may understand why it’s important to have an effective Knowledge Management system in place.
Now it’s time to introduce Innoval’s approach to Knowledge Management which is probably a bit different to what you may have seen before. It’s called a K-Map and it provides a rigorous, structured and repeatable approach. What’s more, we developed it specifically for manufacturing companies, so it’s a practical solution that delivers real value.
Several large aluminium companies already use K-Maps. Therefore, we know our approach works.
K-Map structure
The K-Map is simply a matrix. It provides an overview of the relationships between the quality attributes of the product and the process stages.
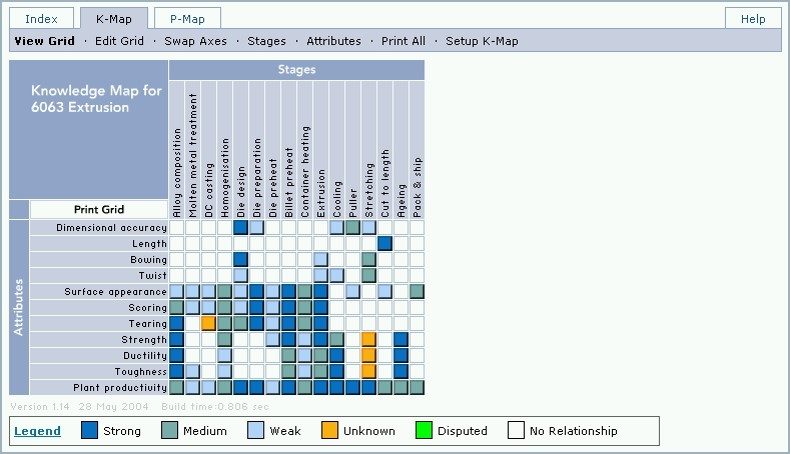
The axis at the top shows the process stages and the axis on the left lists the product attributes. The squares in the matrix show where a process stage affects a product attribute.
The K-Map uses colour to show the importance of each interaction. It can be Strong, Medium or Weak. There are also colours for Unknown or Disputed.
K-Map information
There’s a Summary Level and a Detail Level behind every Process Stage, Product Attribute and Interaction. Consequently, a K-Map stores a HUGE amount of information in one place!
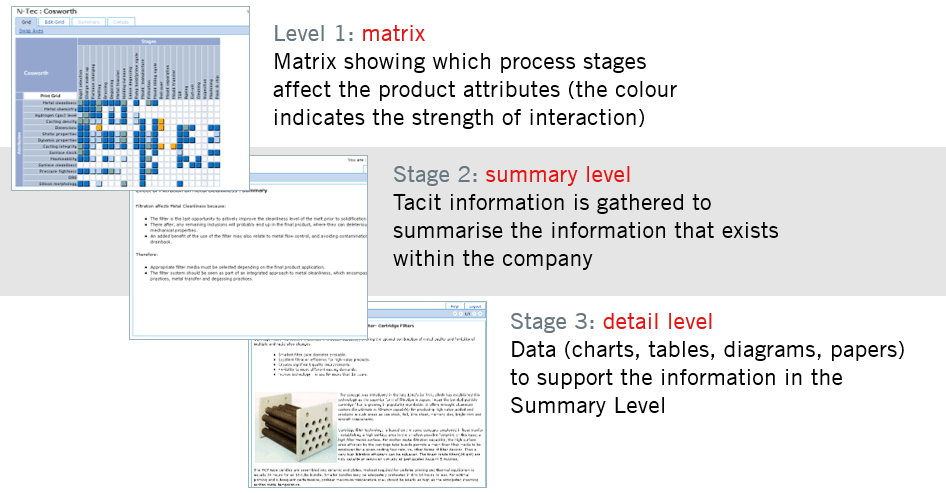
A group of experts determines what goes into the Summary Level.
In the Summary and Detail Levels you can link to documents and web or intranet pages. You can insert images, charts and tables too. Furthermore, the K-Map also records the ‘variables’ of each process stage and what must be done to control them.
New or Existing K-Map?
There are two ways to embark on a K-Map project. You can build a NEW one or you can buy an EXISTING K-Map.
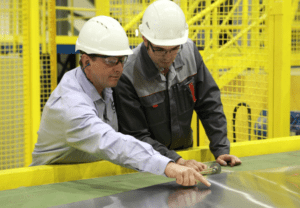
A new K-Map is when we work with you to build a K-Map from scratch via a facilitated workshop.
On the other hand, an existing K-Map is for companies that are new to making a particular product. It incorporates some of Innoval’s knowledge in the Summary Levels. This way you can establish a knowledge ‘baseline’. Consequently, by having this knowledge available to everyone, we hope the learning curve for your team will be shorter.
You can read about one company who bought an existing K-Map for aluminium automotive sheet here.
To summarise, K-Map is a Knowledge Management system with real practical use. If you’d like more information, please have a look at this page. Finally, if you have any questions please send us an email.