Posted on: 14th September 2018 by Kyle Smith
Industry 4.0 is in the press a lot at the moment. It is the latest buzzword (or set of buzzwords) that a company must use if it is to show itself to be at the leading edge of technology. It has generated many conferences across multiple industries, yet the benefits are somewhat nebulous. Indeed, the very concept of a new revolution in technology seems rather vague.
In the first of two blogs about Industry 4.0 I’ll talk about how the term originated, what many people perceive it to be and my own, slightly different, view.
Previous industrial revolutions
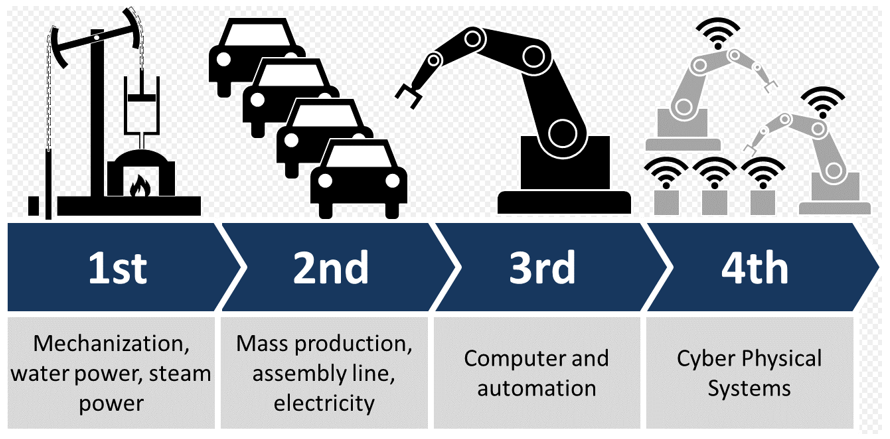
The benefit of hindsight and the perspective of history does at least give some substance to the earlier industrial revolutions. The advent of mechanisation and the utilisation of engines running on water or steam power produced the Industrial Revolution. It resulted in many trade benefits for the leading industrial countries, together with a huge amount of social disruption. This came about as the agrarian economies readjusted and the workforce shifted and moulded to the new ways of working.
The advent of mass production heralded the second industrial revolution. It saw the widespread use of electrically powered machinery, especially in assembly lines. This technological revolution of the late 19th century paved the way for the industrial methods we now take for granted. For example, steel production and the spread of systems such as electricity, water supply and telephones across the developed and developing countries.
The third revolution happened only relatively recently. It comprises the rise of electronics, computers, digital technology, the internet and the increased use of automation to achieve efficiencies.
Is Industry 4.0 the 4th industrial revolution?
Big data, analytics, the Internet of Things, artificial intelligence and robotics are terms we use to describe the current revolution. Some see it as the means by which 50% of the jobs we have today will no longer be done by people. Instead, they’ll be carried out by some form of cyber-physical system.
The building blocks of this “revolution” have been around for some time. In fact, it might be said to simply be the natural output of the third revolution. The great difference is that of the approach and the impact it may have both on our industry and the role of the workers in the future industrial environment.
Many people perceived Industry 3.0 as how “industrialisation + automation” would relieve the burden of manual and repetitive chores. Therefore, it would make the workplace a better and more enjoyable place.
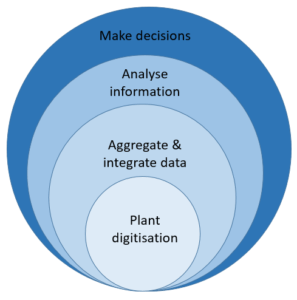
Industry 4.0 now takes this further by making intelligent (rational and hopefully correct!) decisions. These will lead to higher quality products, manufactured at lower cost, using less energy and in a safer working environment. Or at least that’s the theory…
Many suppliers in the industry seek to build up this “revolution” by starting with plant digitalisation. This creates an asset of the data and exploits the value of this asset through big data analysis. The slicing of this data exposes correlations that will hopefully bring more optimal operating conditions.
A different view
In some cases, the need for increased and integrated data collection can be a barrier. In our view it’s not a necessary step to achieving the benefits Industry 4.0 promises. For Innoval, with our deep knowledge of both the products and their requirements, as well as the equipment used in the process route, we envisage a somewhat different path.
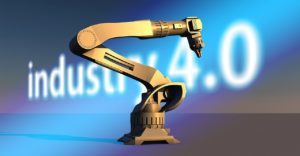
We know full digitalisation is expensive and that data mining can be disappointing. After all, a correlation is not a causation. However, we do have effective models of key process stages that have been built upon robust physical principles and incorporate our depth of knowledge of the underlying materials behaviour.
We can utilise our models to integrate the process and product dimensions. Furthermore, they can identify the key parameters that you need to monitor (and the controls you need to adjust dynamically) to ensure consistent quality and predictable delivery times.
In the next blog I will discuss how the integration of data systems, knowledge systems and process models can lead to the Intelligent Factory. As a result, we could finally realise the benefits associated with Industry 4.0.
This blog post was originally written by Dan Miller who has now left the company. Please contact Kyle Smith if you have any questions.