Posted on: 29th September 2017 by Private: Chris Pargeter
Aluminium hot rolling emulsion undergoes physical and chemical changes in use. This is due to the high temperatures and pressures experienced in the roll bite, as well as contact with the freshly-exposed aluminium surface during deformation. Changes that can potentially occur are:
- evaporative losses
- oxidation and/or polymerisation
- formation of metallic soaps
- contamination with fluids from the rolling equipment
- degradation through microbial contamination
It’s important to monitor such compositional changes and control them to ensure consistent lubricant performance during rolling. Practically, it is important to have good maintenance practices in place. Furthermore, there should also be routine laboratory measurements to ensure stability.
Hot Rolling Emulsion Analysis
Hot rolling emulsion has good cooling efficiency. However, small changes in oil concentration can have a significant effect on the cooling experienced on the hot mill, as well as the lubricating characteristics of the deposited oil.
The conventional way to determine oil concentration is to ‘split’ the emulsion with a mineral acid such as hydrochloric or sulfuric acid. You do this by putting the emulsion and acid together in a flask with a graduated neck, and leave it in a water bath until separation is complete. It’s then possible to use the resulting oil phase for the analysis of specific additives.
Plate-out
The hot rolling emulsion must yield its oil, or ‘plate-out’ on the hot metal surfaces in a controlled manor during rolling. This is to facilitate wetting and adsorption of the functional additives. Emulsion stability affects the plate-out, but it’s possible to monitor it by measurement of the emulsion’s oil droplet size distribution. Techniques typically utilised in the aluminium rolling industry are based on either laser diffraction (Figure 1), or particle counters using the Coulter principle.
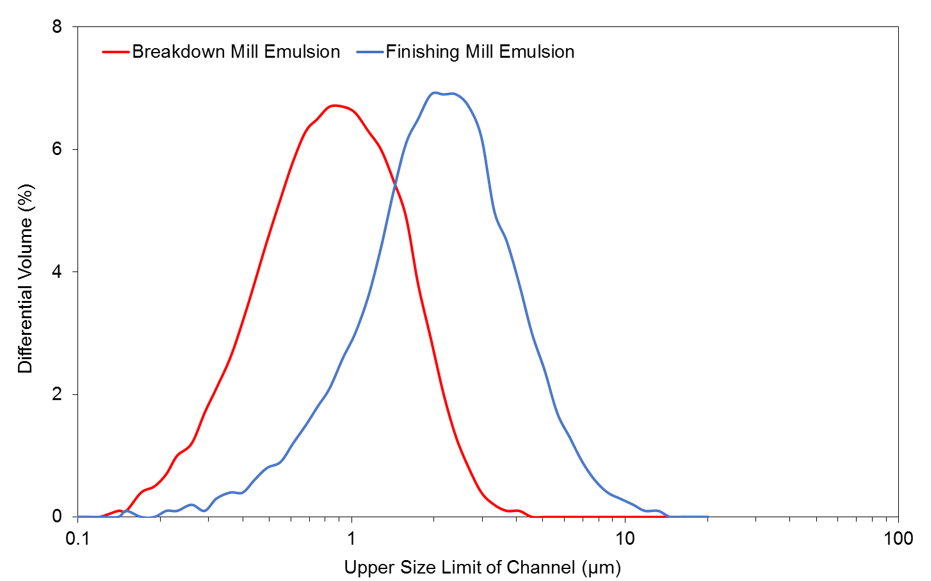
When plate-out occurs, additives form a thin, tightly-packed layer of molecules on the surface. This is to help withstand high reduction loads and protect the aluminium surface during deformation. Infrared spectroscopy monitors the major additives such as organic acids and esters in the oil phase (Figure 2).
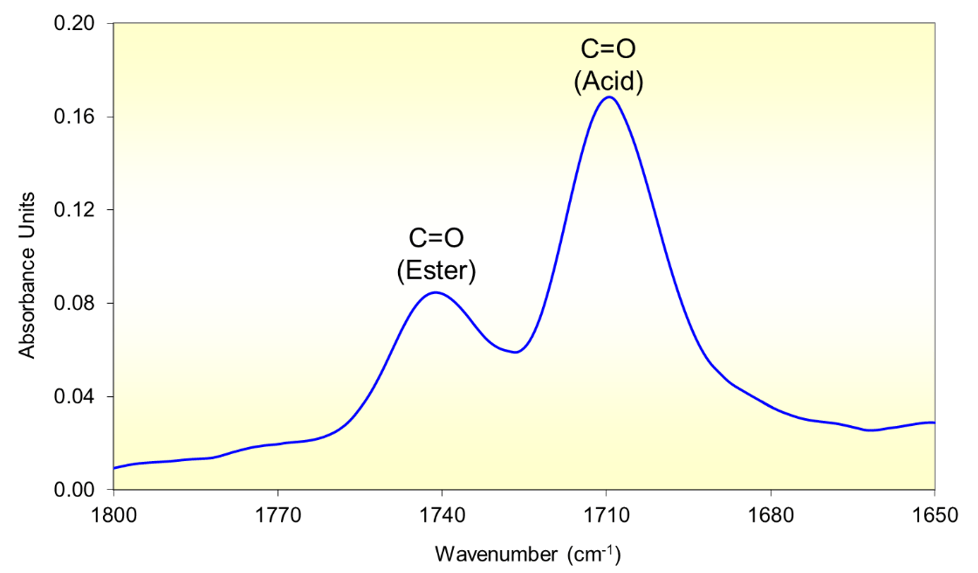
Contamination
The kinematic viscosity of the separated oil phase can potentially highlight contamination by ingress of lubricants from the mill system. You select the viscometer tubes according to the expected viscosity range for the oil phase. The testing temperature is 40 °C.
Ash content (ASTM D482-13) is a gravimetric technique applied to the emulsion to determine the level of inorganic residue within it. The residue may be in the form of insoluble metallic fines generated during rolling. It could also be soluble ash-forming materials that might be present either from the lubricant or from other contaminants.
The emulsion pH and conductivity can affect its stability. In particular, anything that reduces the pH or increases the conductivity can destabilise the emulsion. This will cause the oil to separate. Decreases in pH can occur due to bacterial contamination, while increases in conductivity can be a measure of make-up water quality. It’s possible to use simple, inexpensive probes to quantify pH and conductivity. What’s more, it’s possible to carry out these measurements in-line.
Bacterial contamination can lead to poor performance, offensive odours and corrosion of pipework. However, you can take preventive action, such as through the addition of biocides, before these problems occur if you analyse biological activity. You can use either dip slides or the HMB test (based on the generation of key enzymes by bacteria during biological activity) to do this.
Good control is essential
Analytical control should be viewed as an essential part of the overall quality cycle, and not simply as an overhead cost. Detailed analysis can be expensive and some techniques may involve sophisticated methods and costly equipment that requires skilled operators. Despite this, such costs can often be quite low in comparison to the overall costs associated with production downtime and quality problems.
At Innoval we can help improve your hot rolling process with lubricant/coolant audits and advice on emulsion monitoring. Furthermore, we can train your staff through our aluminium rolling course and on an individual basis. You can read more about our lubrication support here.
(Rolling mill coolant sprays image courtesy of Lechler Ltd.)