Posted on: 1st September 2017 by Kyle Smith
More and more sheet aluminium producers around the world are seeking to quench material at high temperatures. This can increase productivity and have beneficial effects on the metallurgical structure of the metal. However, high temperature strip quenching is one of the hardest processes in the industry to control.
Accurate modelling of strip quenching is critical to optimise the process properly and to adapt to changes in processing parameters.
Factors which affect strip quenching
Quenching during hot rolling uses either mill coolant emulsion or water. Water is an excellent absorber of heat due to its high heat capacity and thermal conductivity. However, its cooling effect is significantly reduced by the addition of oil. Pure water is around twice as effective as a 4% oil in water emulsion. A change in emulsion concentration of only 0.1% can change the strip exit temperature by tens of degrees C.
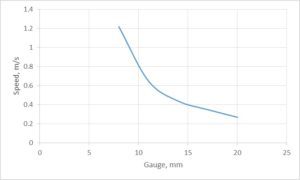
Another important factor is strip thickness. Figure 1 is a plot of the strip speed required to achieve a fixed exit temperature for different thicknesses.
It shows that it’s much harder to quench aluminium strip at gauges above around 12mm. This is because the transfer of heat becomes limited by the rate at which it can be conducted from the core of the material.
The most challenging aspect of the process to describe is the interaction between the coolant and the surface of the metal. The physics at this interface can change dramatically with temperature, making the heat transfer very sensitive to any changes in the process. For example, 1°C changes in coolant or strip entry temperature can lead to changes in exit temperature of tens of degrees. The surface interactions also depend on a large number of process variables, making the physical description very complex.
Heating a pan of cold water – an example
It’s easy to understand the fundamental mechanisms by considering a pan of cold water heated from below. As the pan warms up it heats the water in direct contact with it. Warm water is less dense than cold water, so it rises from the base to the surface. This mixes the water and distributes the heat throughout it.
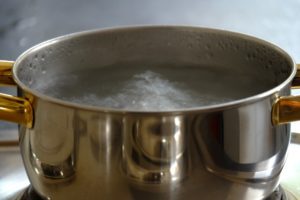
Eventually bubbles begin to form on the base of the pan. At first these re-condense before they reach the surface of the liquid. They form at nucleation sites on imperfections in the material of the pan and rise in columns. They also aid the mixing of the water, which increases the heat transfer from the pan to the water.
As the temperature of the water rises, the bubbles of steam begin to reach the surface. The number of columns of bubbles then increases, raising the heat transfer further, until a maximum is reached. This is called the critical heat flux.
Above this temperature the water becomes full of bubbles and boils violently. This reduces the area of contact between the pan and the water, reducing the heat transfer to the water. If the temperature of the pan increases further, the bubbles merge to become a uniform layer of steam on the surface of the pan. The heat transfer to the water is then at a minimum called the Leidenfrost point. At higher temperatures the only change in heat transfer is due to increased thermal radiation.
Figure 3 is a plot showing how the heat flux through a surface (q’’) varies with the temperature difference between the hot surface and the boiling point of water.
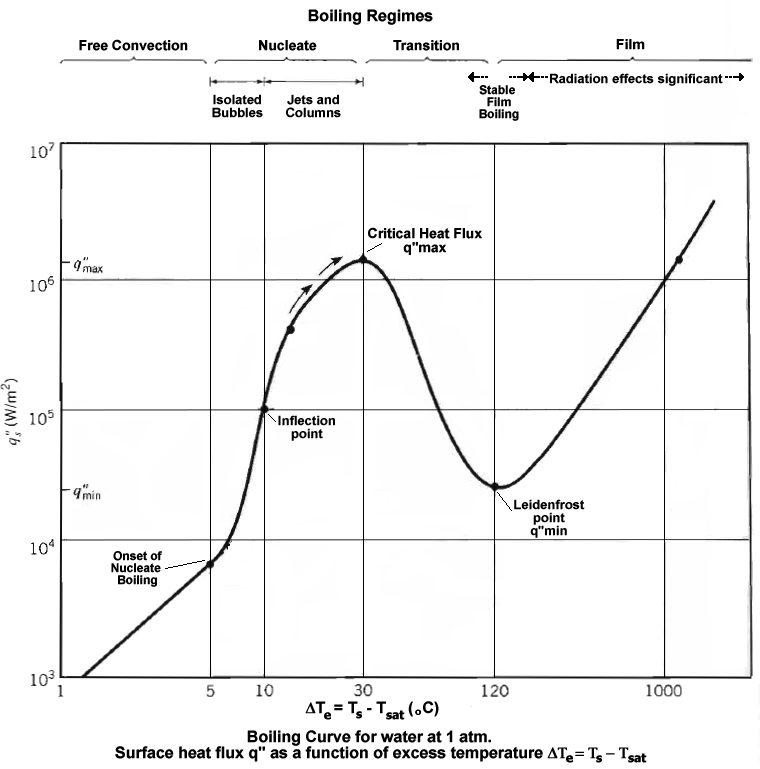
How does this apply to hot rolling?
Hot rolling temperatures are typically above around 200°C. Quenching at these temperatures occurs in the transition and film boiling regimes. The precise form of this curve, however, depends on a wide range of process parameters. These can significantly change the values and locations of the critical heat flux and Leidenfrost points.
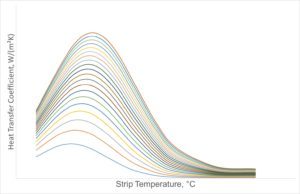
For example, Figure 4 shows plots of heat transfer coefficient with varying strip temperature.
The different curves correspond to different spray intensities, with all other process parameters held constant.
Higher spray intensities shift the peak heat flux and onset of film boiling to higher temperatures.
Physical factors that affect heat transfer
In general the main physical factors affecting heat transfer during strip quenching include:
- surface coolant build up
- coolant effectiveness
- steam production
- Leidenfrost and critical heat flux points
- amount of pool cooling
The process variables which influence these factors include:
- strip temperature
- strip speed
- spray intensity
- spray pattern
- droplet size
- droplet velocity
- coolant temperature
- emulsion concentration
Innoval Quench Model
It is clear, therefore, that this is a challenging process to model. However, it is precisely the complexity and sensitivity of the process which makes the modelling of it so important. It is for this reason that a great deal of care has been taken in the development of the Innoval Quench Model.
This unique tool has sufficient complexity and accuracy to be able to produce excellent predictions for strip quenching in any regime. If you’d like more information about the Innoval Quench Model, please contact me.
This post was originally written by Dr Timothy Clemson who has now left the company. Please contact Kyle Smith if you have any questions.