Posted on: 23rd August 2018 by Vicente Martin
The process of creating a coil of thin foil in a foil separator is probably one of the most extreme cases of coiling. For example, a seemingly small coil of 6 micron foil can have over 30,000 laps wound onto a spool. This enormous number of laps creates very high radial pressures which affect the stickiness of the inner laps.
Foil manufacturers try to control coil density through the build up by using tension and pressure curves. However, the real stress state of the foil deep into the coil is not known. This is because it changes with each new lap wound onto the coil. Equally, the stress state inside the coil after further processing, like after anneal, is usually just estimated.
The Innoval Winding Model
The Innoval Winding Model is able to calculate the development of coiling stresses with a large number of laps. Furthermore, it can do so within a reasonable computing time. It therefore offers us a clearer insight into what the influence of different coiling strategies, or different coil set-up arrangements on the foil separator, would be.
In order to illustrate our model capability, we have simulated the coiling of a 1616 mm wide, 6.3 micron foil onto a steel 300 mm core. We have set the tension and pressure to a very simple strategy. This is to highlight the impact of the core on coiling stresses. The diameter of the simulated coil is 700 mm. The calculation has been carried out with over 32,000 laps.
Core stiffness effects in the foil separator
We have compared the effect of the stiffness of the core on the stresses in the inner parts of the coil by changing the thickness of the steel. This is a possible variable in foil plants to reduce the cost of the cores. Thinner walled cores are cheaper.
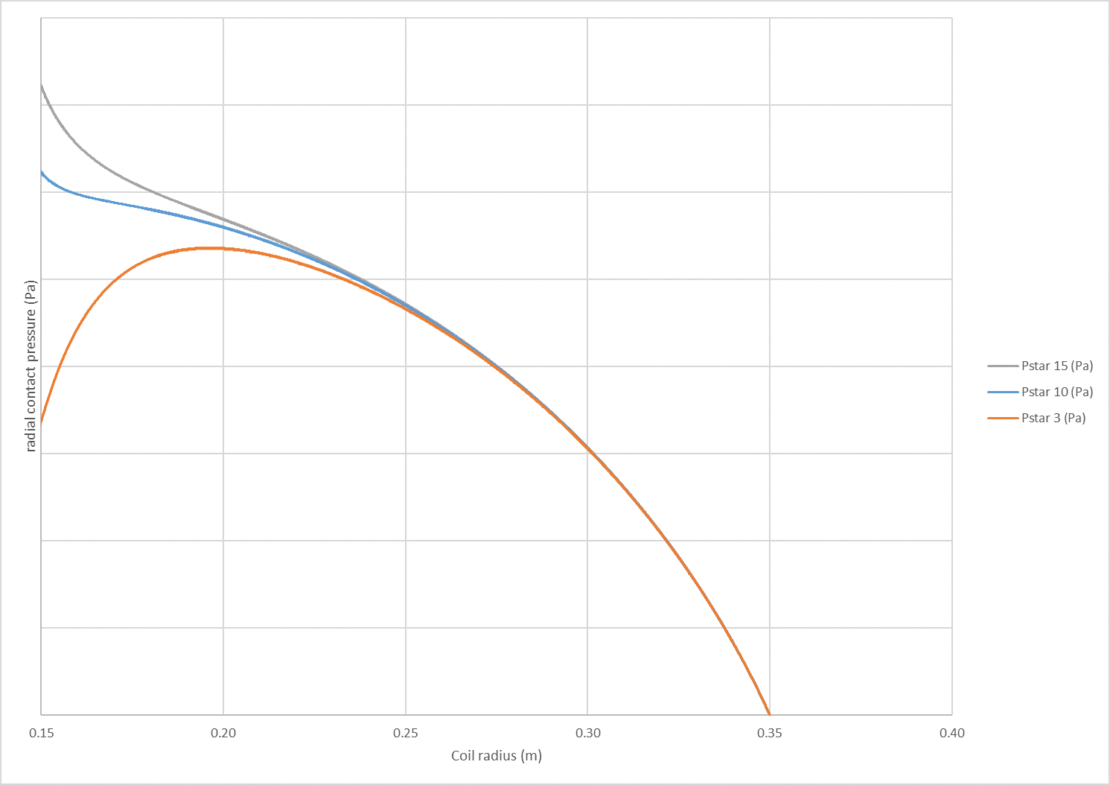
As expected, as we wind the coil and add new laps, the radial pressure inside the coil grows to very high values. There is, however, a difference in behaviour depending on how stiff the core is. Stiffer cores raise the pressure on the laps close to the core. On the other hand, less stiff cores can actually have the effect of relieving pressure. This would have implications on the tendency of the material to stick in this area, making it less likely to have problems.
Elastic deformation
It is interesting to note that the pressures developed inside the coil are high enough to elastically deform the aluminium. Therefore, apart from changing the inter lap contact condition, elastic deformation of the material can lead to a small changes of thickness. As a result, over time, there could be permanent changes due to creep. You can see this in Figure 2.
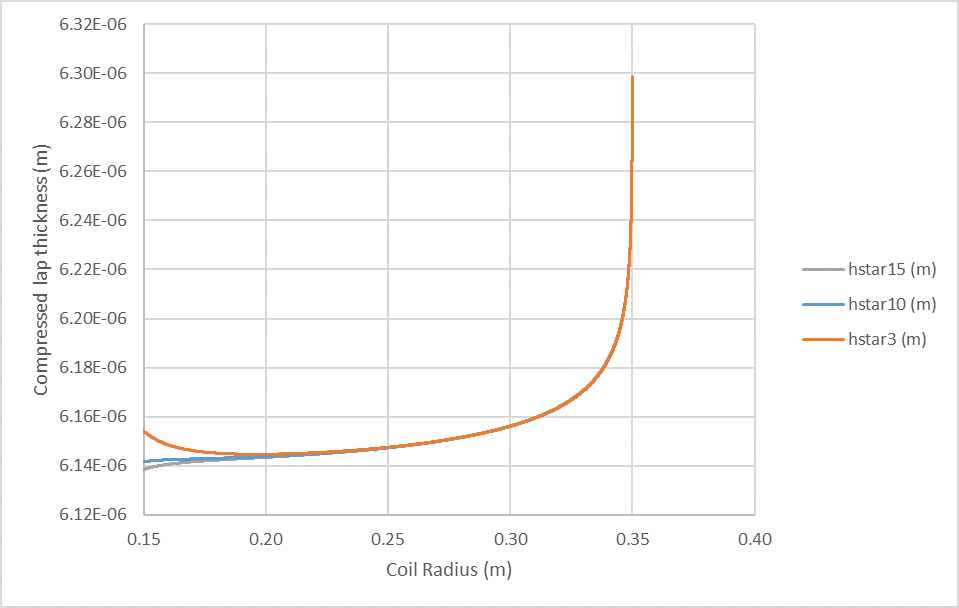
We might be tempted to conclude that a lower stiffness core would be beneficial to the quality of the final coil. However, the situation is different if we look at the development of circumferential stresses.
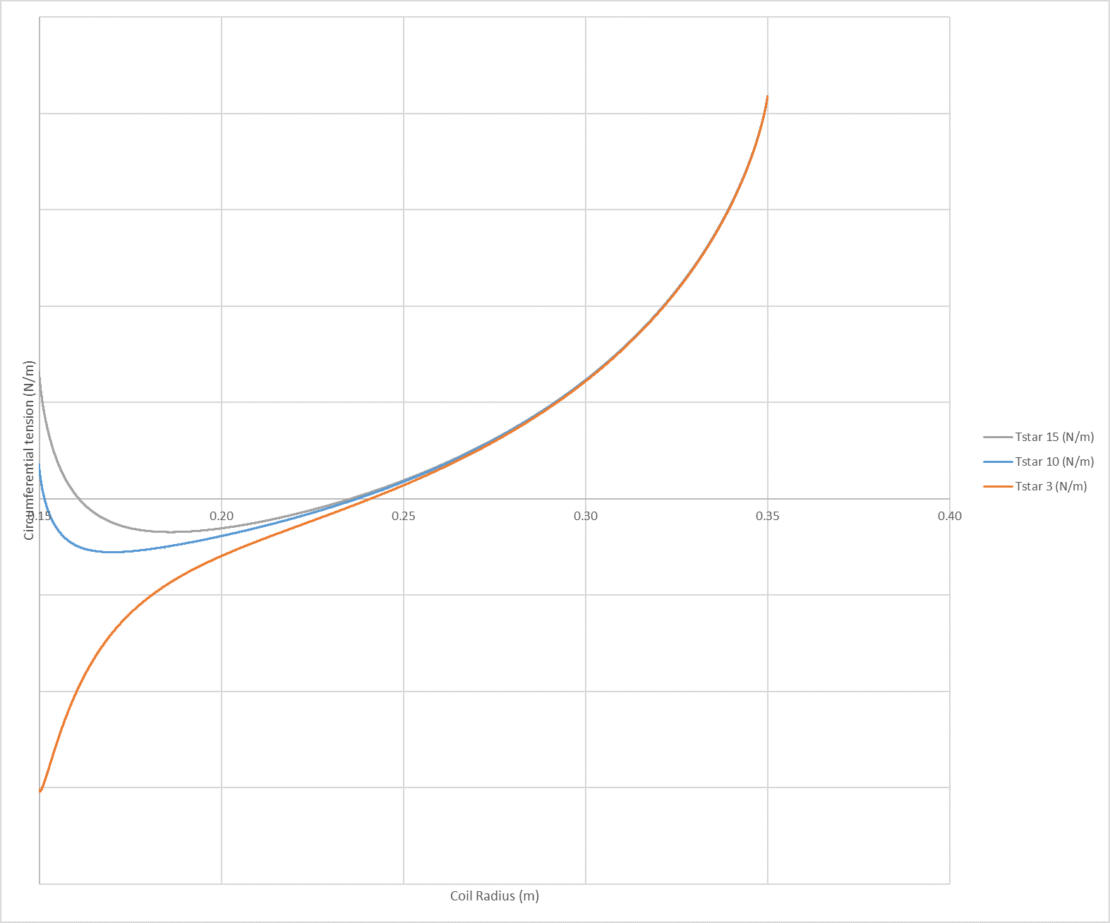
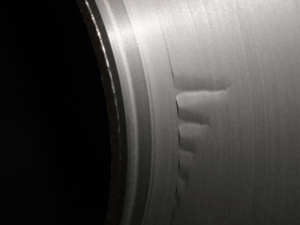
As you can see in Figure 3, the inner laps move into a state of high negative tension. This can result in the development of buckling defects, or v’s, in the inner parts of the coil, Figure 4.
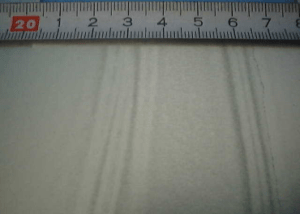
Furthermore, it will be a contributing factor in the occurrence of inter lap movement and fretting corrosion near the core, Figure 5. In this case, lower stiffness cores would tend to increase problems with fretting corrosion later on.
A powerful tool
As you can see, the Innoval Winding Model is a powerful tool to understand the stress state of a thin foil coil. It can also help you to explore the impact of process changes to your foil separator. You’ll understand more how the changes affect the quality and reliability of the coils you send to the laminator plants.
Please contact us if you’d like more information about any of our process models.