Background
W H Tildesley, based in Willenhall in the UK, has been producing high quality forgings for over 150 years. They specialise in small and medium batch production in a wide range of modern materials. Major investments in 3D modelling, simulation software and state-of-the-art in-house die-making capability mean that cost-effective forgings can be produced in small quantities.
As part of their continuous improvement programme, W H Tildesley enlisted the help of Richard Keyte to further improve the production of aluminium forgings by examining their thermo-mechanical process route.
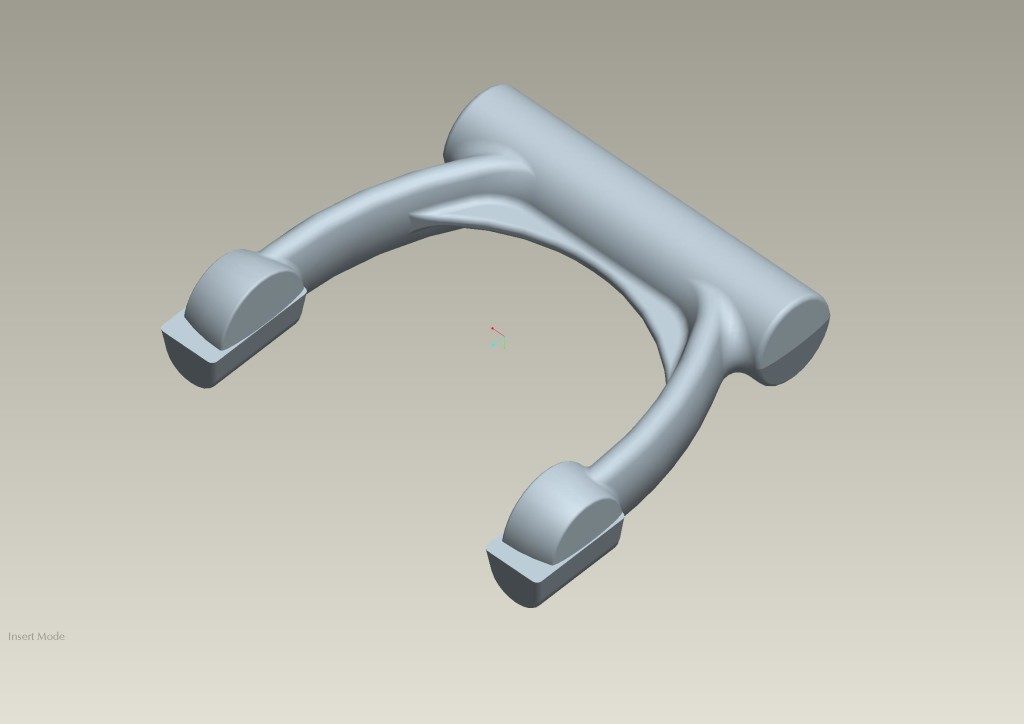
How we were involved
At W H Tildesley our work focused on, amongst other things, furnace temperature control, die heating procedures, and racking and stacking practices in the pre-heat furnaces.
Richard, who was part of our Materials Development team, analysed the whole thermo-mechanical process route at the plant in Willenhall and then set about optimising it.
Our Materials Development team has extensive knowledge of microstructural development during processing and its effect on product performance. We also understand surface modification during finishing operations. By working with us, clients gain an in-depth understanding of where in their process these are controlled so they can ensure a consistent, quality product.
Services Involved
- Materials Development
- Process Improvement
This case study appears as an article in the 2008 edition of ‘innform’; the newsletter of Innoval Technology.
Richard has given us a greater understanding of the factors we need to consider when processing aluminium. As a result of his involvement, we’ve seen the scrap rate of one of our most challenging aluminium components drop by 85%.
John Tildesley, Managing Director of W H Tildesley