Background
To serve our clients in the best way possible, it’s important that we know about the latest, cutting-edge developments in aluminium. To this end, we’ve been involved in collaborative R&D projects, funded by the UK Government’s Innovate UK (and also by European-funding through FP7 and Horizon 2020), for the last 10 years. Most of these projects have had an automotive focus, and one such example is lightweighting technology via the UlCab project.
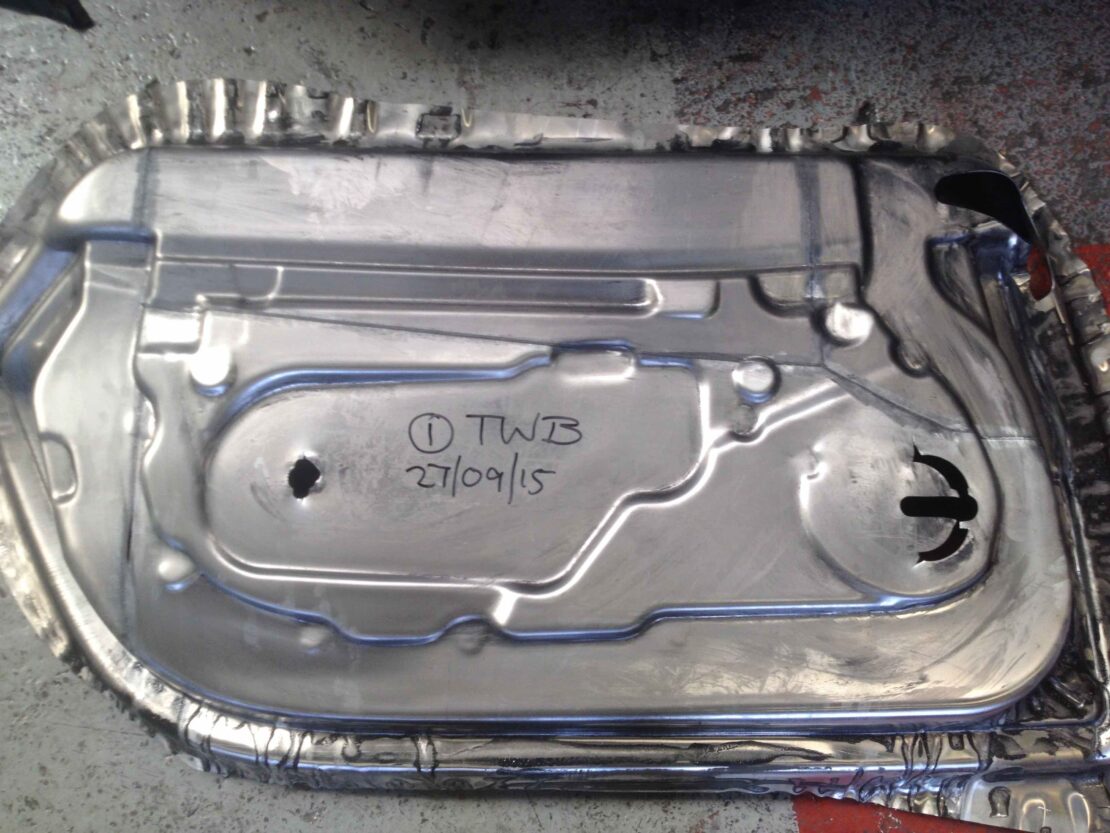
The aim of UlCab (Ultra-light Car Bodies) was for a consortium of industry leaders – PAB Coventry, Impression Technologies, Imperial College London, Innoval Technology and Lotus Cars – to develop a lightweighting technology for significant reduction in carbon emissions from vehicles.
The project centred on two techniques being combined into one process; tailorwelded blanks and HFQ® (Hot Form Quench). HFQ® is a patented hot forming process developed by Impression Technologies, based on research at Imperial College London, for enhancing the formability of high-strength aluminium alloys. This technology provides a greater draw depth and allows sharper bend radii, both of which enable pressings to be manufactured in aluminium that were not feasible before.
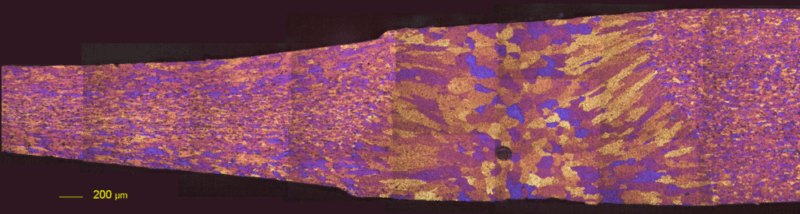
The combination of tailor-welded blanks and HFQ® enables aluminium sheets of two different thicknesses to be formed into one part. At present, forming a sheet containing welds at room temperature will cause the welds to crack. However, if it is done at the solution heat treatment temperature, the welds behave like the rest of the sheet and do not crack. There is no heat affected zone associated with the weld and no loss of mechanical properties.
How we were involved
As part of the UlCab project group, Innoval’s materials team provided information on alloy selection at the very start of the project. We also developed a simple mechanical abrasion technique to prepare the sheets for welding, and we evaluated the quality of the laser welds using optical and electron microscopy. The success of the project enabled Impression Technologies to develop a commercial HFQ®-formed tailor-welded solution and produce proof-of-concept panels at consortium partner PAB’s facility in Coventry, UK.
HFQ® is the registered trademark of Impression Technologies Ltd
Services Involved
This case study appears as an article in the 2016 edition of ‘innform’; the newsletter of Innoval Technology.
Innoval brought a unique understanding of automotive aluminium sheet to this project. Their analytical capabilities, as well as their expertise in aluminium joining and surfaces, were key to the success of the UlCab project.
Dr Alistair Foster, Chief Technology Officer, Impression Technologies
In addition to the technical expertise that Innoval brought to the project in terms of sheet metal analysis and joining capabilities, they were a pleasure to work with in project management terms. They were always willing and more than able to help with any task that the project required, and helped the project partners form a successful and dynamic working group.
Adam Malone, R&D Project Manager, PAB Coventry