Posted on: 26th March 2020 by Kyle Smith
When manufacturing sheet products it’s important to understand the rolling force. This is because you need it to set the appropriate roll gap on the mill, accounting for the stretch of the stand.
The prediction of rolling force can be challenging due to the large number of inter-connected process variables involved. However, many years of experience working with rolling mills has allowed us to create the Innoval Rolling Model which gives accurate rolling force predictions.
Factors which influence the rolling force
Yield strength
The main factor influencing the rolling force required to reduce the thickness of strip in a rolling mill is the yield strength of the material being rolled. The calculation of yield strength depends upon a wide range of factors. These are:
- composition
- previous work done on the material
- thermal history
- speed of rolling
- change in thickness
We use what’s known as a constitutive equation to calculate the material’s yield point, or flow stress. There are many forms of these equations in the academic literature, and physical metallurgy is the basis of most of them. However, in general these equations all have a similar form:
Yield stress = (Strain hardening factor) x (Strain rate hardening factor) x (Thermal softening factor)
In the rolling of aluminium, it is strain hardening which typically dominates at low temperatures. On the other hand, strain rate and temperature are more important in hot rolling. The alloying elements and the state in which they exist within the material influence each of these factors. Therefore, a good understanding of the thermal history and resulting metallurgical properties is imperative to the prediction of yield strength.
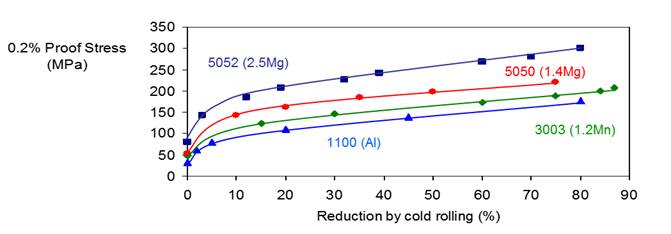
Friction
We can calculate the resulting pressure on the rolls from the deforming material once we’ve calculated the flow stress at a given point within the roll bite. However, the friction between the two surfaces also plays a part, especially in cold rolling. Consequently, we must understand the microscopic interactions between the lubricant, rolls and material. This means knowing about the roughness of the surfaces and the temperature-viscosity relationship of the lubricant.
Neutral Point
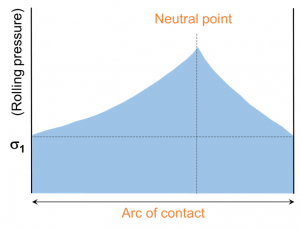
In standard cold rolling, pressures developed within the bite increase towards the middle of the bite from the entry and exit. They peak at a point known as the neutral point, where the speed of the rolls is precisely matched by the speed of the material. The location of this point determines the total rolling force and is strongly influenced by the tension on the strip either side of the bite. To find its location, we need to calculate the rolling pressures from the entry and exit until their values match at some point within the bite.
At very thin gauges the neutral point becomes spread out into a neutral zone and the roll is flattened into a more complex shape, requiring alternative calculations. At very thick gauges, the situation is different too. The effects of the through-thickness flow become more important and require a third approach to rolling load calculations.
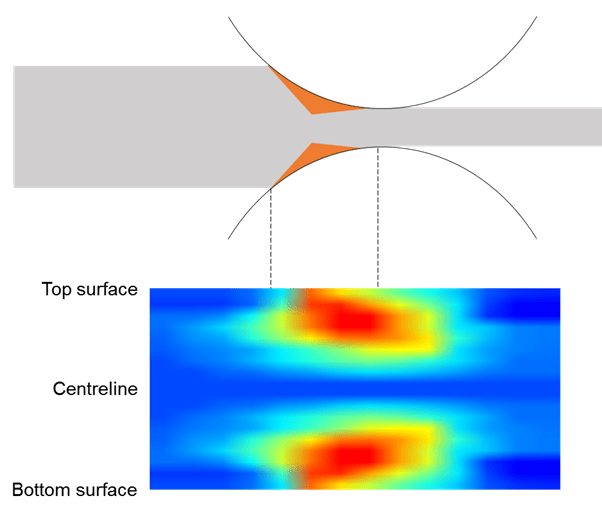
Tension
The tension applied to the strip also influences the rolling pressures developed within the bite. Higher entry tension lowers the starting point on the friction hill and so needs to be taken into account in the rolling model.
Further learning
In summary, the calculation of rolling force is a complex and multi-disciplinary calculation. Changes to one process variable inevitably influence others, and the effects can often be counter-intuitive. For these reasons, the Innoval Rolling Model is an invaluable tool in our day-to-day consulting business. It is also available to purchase, enabling the refinement of process schedules and the simulation of potential new products and equipment.
We discuss all of these topics, and much more, on our Aluminium Rolling Technology Course. Participants of the course take part in an insight-packed week of lectures from our highly experienced team of rolling consultants. There’s more information, including a registration form, in the link above and you can see an example timetable here:
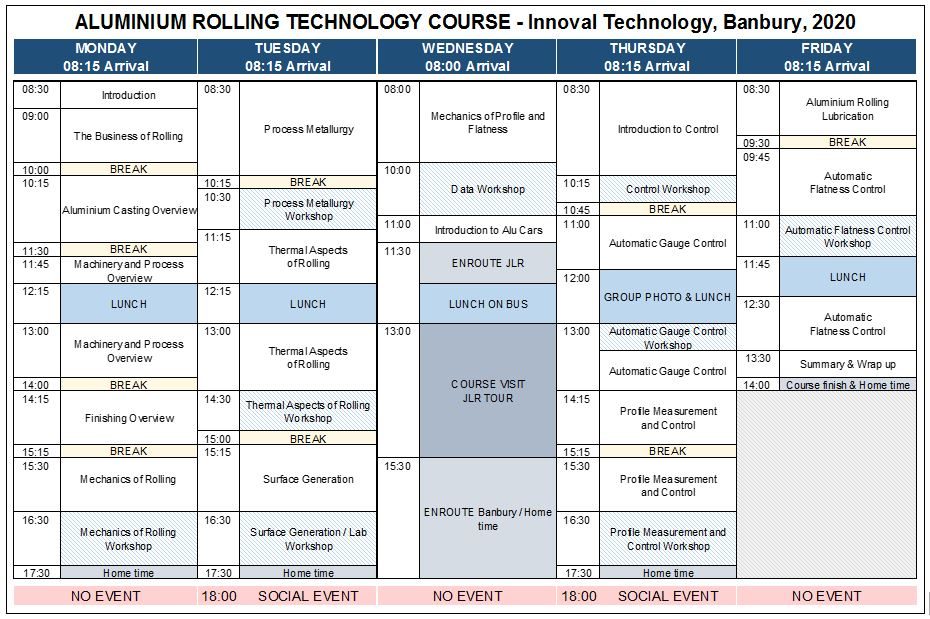
This post was originally written by Dr Timothy Clemson who has now left the company. Please contact Kyle Smith if you have any questions.