Posted on: 13th July 2018 by Dr. Junjie Wang
This blog is the first in a series about aluminium surface cleaning. I’m going to provide a very brief overview of aluminium surface cleaning which will serve as the basis for my next posts. These will be about evaluating levels of cleanliness on aluminium sheet surfaces.
Aluminium rolled products feature heavily in industry. Over the last decade we’ve witnessed significant growth in the use of aluminium sheet in the automotive industry. This is to reduce vehicle weight for improved fuel economy, to lower emissions from fossil fueled vehicles, and to extend the driving range of electric vehicles.
Why do we need to clean the surface?
In most applications, we must chemically or electro-chemically clean aluminium rolled products. This aluminium surface cleaning is to remove residual mill oil, smut, surface oxides and, most importantly, the near-surface disturbed layer so as to provide a uniform surface to receive pretreatment.
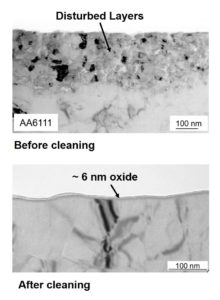
Hot and cold rolling generates the near-surface disturbed layer. This is due to the severe shear strain in the near-surface region from the interaction between the aluminium surface and the steel rolls.
The disturbed layer contains nano-sized grains with grain boundaries decorated and pinned by oxide particles and lubricant residues.
The removal of the near-surface disturbed layer is critical for the pretreatment to be successful. With good pretreatment you can guarantee good corrosion resistance after coating and the long-term durability of adhesive bonding. Therefore, effective cleaning is vital to the performance of aluminium automotive sheet.
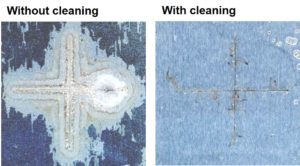
The different types of surface cleaning
Cleaning is either a coil or a batch process. The main difference between coil cleaning and batch processing is in the very limited time available for coil cleaning. In this case, the treatment time is in seconds rather than minutes. In this blog I will talk about coil cleaning.
The coil cleaning processes used for aluminium alloys differ in terms of the solution chemistry used, the method of applying the solution and whether or not an external current is applied.
Acid or alkaline cleaning solutions
Acid cleaning processes are usually based on sulphuric (H2SO4) or phosphoric (H3PO4) acid solutions and surfactants. However, hydrofluoric acid (HF) is usually added as an activator. Typical acid cleaning operating temperatures are in the range of 50 – 70 °C for contact times of 5 – 60 seconds.
Alkaline cleaning processes are based on sodium hydroxide (NaOH) solutions. Typical operating temperatures are in the range of 50 – 70 °C for contact times of 5 – 20 seconds. It is a fast etching process compared to acid cleaning. However, solid precipitates form in the bath and waste (aluminium hydroxide) has to be managed. Some oxide particles and intermetallics, which are insoluble in the alkaline solution, form a ‘smut layer’ which loosely attaches to the aluminium surfaces. As a result, alkaline cleaning must be followed by an acid de-smutting step.
Immersion or spray application
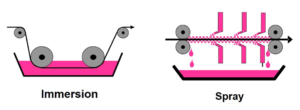
Both acid and alkaline cleaning can be applied by immersion or as a spray. In both cases a multi-step water rinse follows the cleaning stage to thoroughly remove the cleaning solution from the aluminium surfaces.
Electrolytic or chemical cleaning
Acid or alkaline cleaning is a chemical process. Acids like sulphuric acid and phosphoric acid are relatively good cleaning agents on their own. However, electrolysis can increase their cleaning power considerably.
The mechanism and the process of electrolytic cleaning in these acids is similar to anodising. For anodising, the process generates the characteristic anodic oxide film with regular pore structure on the aluminium surface. The oxide film development is a competition between film growth and dissolution. By controlling acid concentration and temperature, along with the anodising voltage, it is possible to make the aluminium oxide dissolve at the same rate as it is formed. This is electrolytic cleaning.
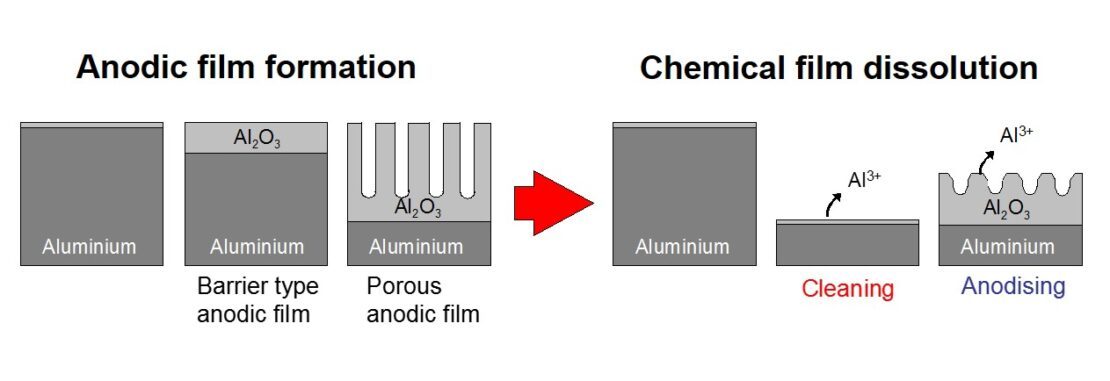
The electrolytic cleaning does not need HF which is good news for health and safety and the environment. Furthermore, the process is very fast and flexible. For example, an effective cleaning with minimal residual oxide can be achieved in 0.5 – 3 seconds. What’s more, the equipment can also work as an anodising pretreatment line.
Despite these many advantages, there are not many aluminium surface cleaning lines in industry using the electrolytic cleaning process. This is highly disappointing.
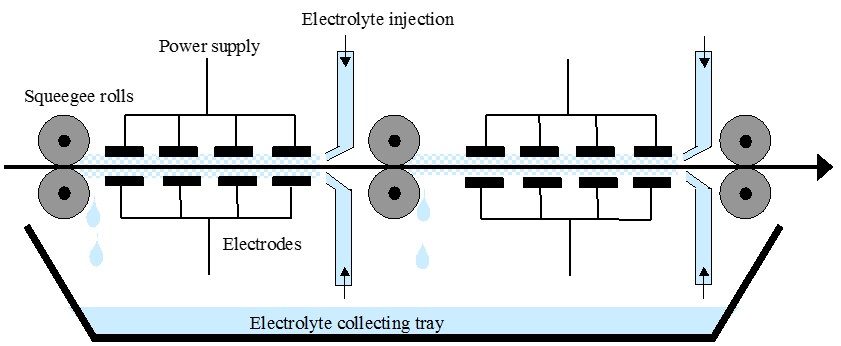
Optimised aluminium surface cleaning systems
Many of the cleaning and pretreatment systems on the market today originally came from the steel industry. At Innoval we have a thorough understanding of how these treatments can be optimised for aluminium. What’s more, we’re able to examine your product surface after each process step to make sure both the cleaning and pretreatment are working properly. You can read more about this here.
Cleaning, pretreatment and corrosion are just some of the topics we cover in our Aluminium Automotive Sheet Training Course. If this course sounds interesting to you, please ask us for further information.
Finally, as I mentioned at the start, I’ll explain about evaluating surface cleanliness in my next blog.