Posted on: 21st February 2020 by Dr. Junjie Wang
Surface quality is very important for many aluminium products. It can impact product performance in areas such as bond durability, corrosion resistance and coating adhesion. One of our previous blogs discussed aluminium surface analysis using transmission electron microscopy (TEM) and explained why we need to understand the aluminium surface. You can read it here.
In this blog I’m going to discuss using high resolution low accelerating voltage scanning electron microscopy (low-kV SEM) to examine surface quality.
Benefits of using low-kV SEM
Scanning electron microscopy (SEM) makes use of signals produced from the interaction between an electron beam and a sample surface. The signal is collected from the interaction volume of the electron beam in the sample. For a given sample, the voltage used to accelerate the electrons determines the interaction volume.
When operating at a low voltage (< 5kV), the interaction volume decreases and shrinks towards the outer surface. This means the collection of signals is only from the outer surface layers. Therefore, the images obtained have more detailed information of the surface morphology and chemistry of this outer layer. This is critical for aluminium surface analysis.
Another benefit is that low voltage minimises the charging effect on non-conductive samples. Electron build-up on the surface of non-conductive samples, such as lacquered cans, causes charging which can make imaging difficult or impossible. In addition, low voltage operation can also increase resolution.
Applications in aluminium surface analysis
Surface plan-view
In the automotive or canning industry, a pretreatment film is normally applied to the aluminium sheet to keep the surface stable and to improve adhesion. Automotive OEMs and can manufacturers usually put requirements on coat weights of the pretreatment film. However, surface analysis not as simple as that. The right coat weight does not necessarily mean that the pretreatment is sound. The continuity and uniformity of the pretreatment film are always the key factors that control the performance.
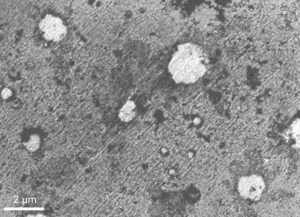
Figure 1 shows circular defects in the thin organo-phosphonic acid based pretreatment on an aluminium automotive alloy surface. The pretreatment is significantly thinner or even absent in these circular features. This is due to blistering of the pretreatment film due to reaction with water vapour.
The accelerating voltage used to take the image was only 500 volts. If we’d used a high voltage, such as 20 kV, we wouldn’t be able to see these features as the film is only a few mono-layers in thickness.
Sample preparation
At high voltages like 20 kV used in conventional SEM, the edge and the near-surface region of a sample in cross section usually lose contrast when taking images. However, operating at low voltage can minimise this edge effect.
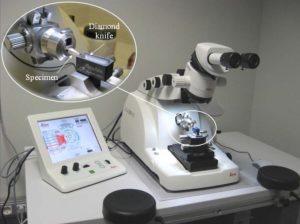
We use ultramicrotomy to prepare cross-sectional samples and Figure 2 shows our setup for ultramicrotomy. In the 1970s, ultramicrotomy transferred from the biological field to preparing thin electron transparent sections of surface films on aluminium. Today we use it as a standard technique for preparing samples for surface film analysis.
It’s possible to produce cross-sections from almost anywhere on the sample surface, such as at the location of a surface defect. Figure 3 shows the microtomy process schematically. A pyramid shaped sample with a smooth tip across the site of interest is most suitable for SEM examination. The cut-off thin foil slices are suitable for TEM examination.
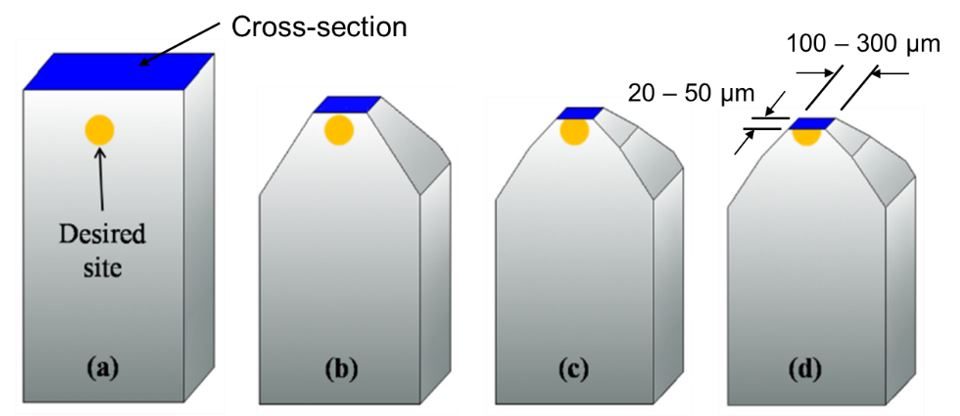
Examination of cross sections through surfaces
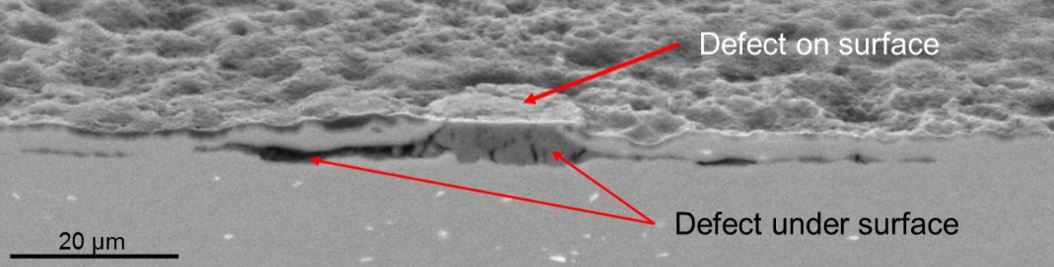
The upper half of Figure 4 shows a protuberance of about 20 µm diameter on an anodised and coated lithographic sheet sample. The lower half of the image shows the cross-section through the protuberance. This shows that oxidation/corrosion occurred underneath the protuberance and, as a result, there’s sub-surface cracking extending to about 100 µm.
In another one of our blogs, I explained why effective surface cleaning is critical for aluminium rolled products. The key purpose is to remove the near-surface disturbed layer. You can read it here.
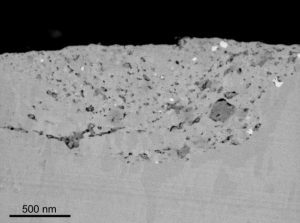
Figure 5 shows the varying thickness of a disturbed layer on an ultramicrotomed AA5182 automotive sheet surface cross-section. You can see micro-cracks and a high population of oxide particles (dark spots) and intermetallic dispersoids (bright spots) within the disturbed layer.
These are typical examples of how the combination of ultramicrotomy and low-kV SEM techniques can help to understand the surface/sub-surface of aluminium products.
Evaluating your aluminium surface quality
Like the TEM observations discussed in our earlier blog, we’ve found that low kV SEM observations are invaluable. Consequently, we use these techniques on a daily basis to analyse aluminium surfaces, pretreatments, coatings and their interfaces. This gives us a deep understanding of what is important, and why the surface/interface of aluminium products might fail in testing or in service.
The Materials Testing team at Innoval offer all the aluminium surface analysis techniques described here. We either use our in-house equipment or use the microscopy equipment at nearby universities. With these capabilities we can get to the root cause of most aluminium surface problems, including corrosion problems.