Posted on: 3rd December 2015 by Kyle Smith
The performance of an aluminium rolling mill will be a combination of several key parameters including mill productivity and product quality from the mill. The performance will decline for many reasons as the mill ages and these will be discussed below. However, it is also important to consider the development of performance in a new rolling mill and how this can decline for comparable reasons which must be controlled to maximise the benefits from such a capex investment.
When the mill commissioning period ends there may be a drop in performance as the client takes complete control of the mill, rolling without the experienced support of the supplier’s engineers before the client is fully used to all new features, and because the client may also start to roll a wider mix of products compared to those defined by the guarantee tests. Gradually performance recovers as the client optimises the process. It is worth noting that when the client buys a Danieli aluminium rolling mill, Innoval Technology can be on-hand to support the client during this difficult post-commissioning phase to ensure faster and continued improvement in performance up to world-class levels.
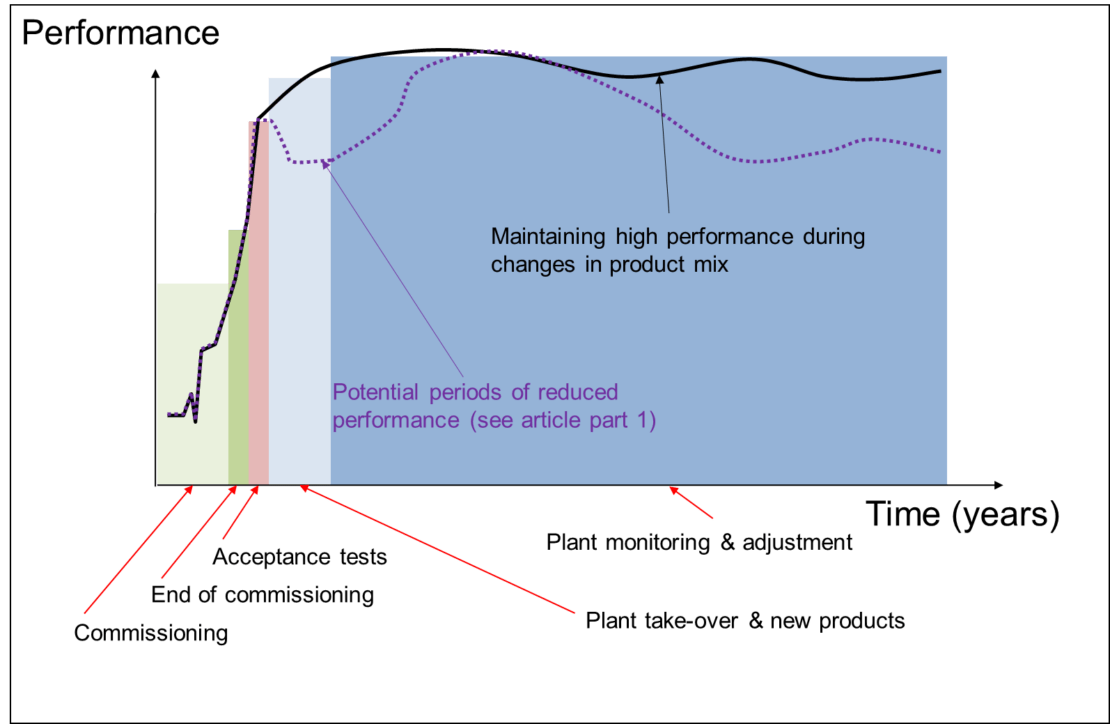
Once peak performance is achieved, there is always a need to counter any issues arising that will lead to a decline in performance if left unsolved. Often performance will decline over several years and this will trigger campaigns of mill optimisation to return performance to previous high levels. This post identifies and discusses some of the factors that can result in a declining mill performance.
There are several reasons why an aluminium rolling mill’s performance declines. As the mill is utilised more, the owner will push the mill to its limits, increasing speeds and reductions. At the higher values, the ancillary functions of the mill may perform less well and problems with surface quality, oil carry-over and ironing roll control may become constraints. Moreover, during a period of years, the product mix may change, the customer specifications are likely to become tighter and competition from home and abroad requires cost cutting and product differentiation. Unless the plant has the skills to adjust the tuning parameters of the mill’s on-line control systems, an aluminium rolling mill that was tuned at the time of commissioning may not meet the desired quality requirements of the new products. External support may be required to retune control systems to achieve high levels of performance.
If you’d like to know more about how we can support your aluminium rolling operation, click here
Did you know that we run a training course specifically about aluminium rolling technology? It’s the only one of its kind and it takes place twice a year here in Banbury, and also online. You can read about the course here and also download a registration form.
This blog post was originally written by Dan Miller who has now left the company. Please contact Kyle Smith if you have any questions.