Posted on: 14th March 2016 by Prof. Geoff Scamans
It has become glaringly apparent, following the VW “Dieselgate” debacle, that there is a large and growing divergence between the measured CO2 emissions and what actually happens when cars are driven on the road. This means that the vehicle OEMs are much further away than we all thought from delivering CO2 reduction from our cars, and that the legislated requirements for 2020 and beyond will be much more difficult to achieve if realistic testing becomes the way of measuring actual CO2 vehicle emissions.
The OEMs are however being given wriggle room as, although the now obsolete NEDC (New European Drive Cycle) test method will be replaced by the more realistic WLTP (Worldwide harmonized Light vehicles Test Procedure) in 2017, the CO2 targets will be softened to allow manufacturers time to cope with the more demanding actual emission based requirements. We may still be many years away from realistic vehicle testing and regulation based on these measurements, but they will both come and will make life very challenging for all OEMs unless they make their emission reduction technologies much more effective.
Emissions reduction was going well…
In terms of historical perspective, following the mandatory CO2 regulation for cars introduced by the EU the measured emissions on test fell at about 1%/year from 2001 to 2008 and then improved to an average of 4%/year after 2008. Everything apparently looked to be in order as the average CO2 emissions from new cars reached 123 g/km that was well ahead of the 130 g/km legislated requirement of 2015.
…but then it all changed
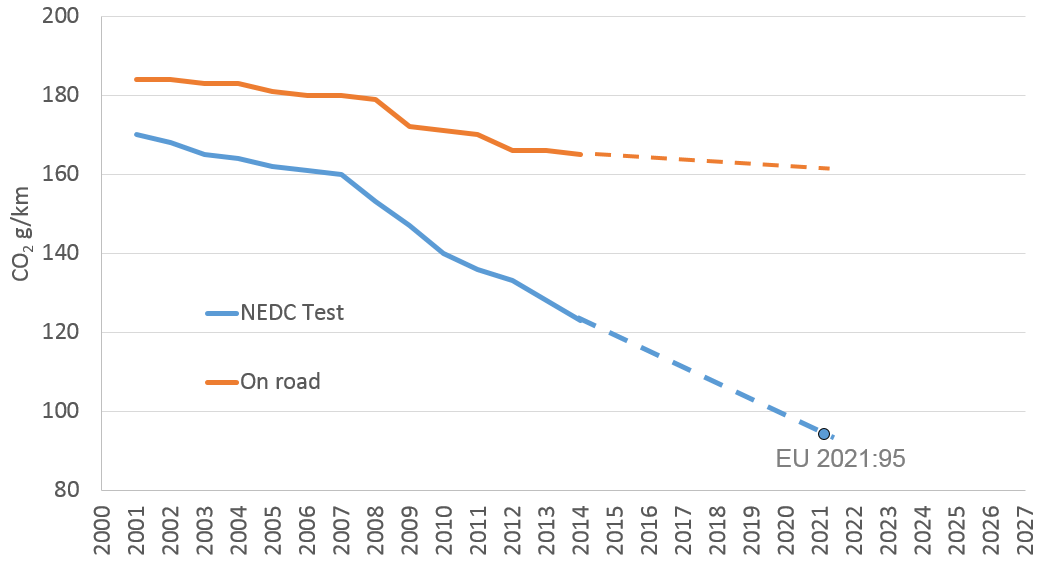
This situation has now changed dramatically as we are now aware of the divergence between the measured values and the on-road vehicle performance. This means that today vehicles falsely qualify for lower rates of taxation as these rates have been based upon the emissions data published by the car companies, which we now know is unrealistic. Consumers may now have to anticipate a hike in tax if ‘on the road’ figures are to be used. Furthermore, the average vehicle owner will pay about £400/year more in fuel than they thought they would from their car’s data sheet.
It’s a similarly sorry tale for the environment. Whilst we have thought that average vehicle emissions reduced by 27% from 170 g/km in 2001 to 123 g/km in 2014 they actually only fell by 8% from 184 g/km in 2001 to 168 g/km in 2014 when actual emissions data is used. The divergence issue affects all classes of vehicle, all manufacturers and all diesel, petrol and hybrid vehicles. More alarmingly, the divergence in real and test performance is largest for hybrid vehicles.
Future aluminium lightweighting challenges
Multiple emission reduction technologies have been identified but far and away the most important and effective and relevant reduction technology is vehicle lightweighting. This CO2 reduction technology will get the largest boost from the new situation as most of the simple lower cost alternative technology options have already been exploited. The focus on lightweighting will progressively switch from the body-in-white to chassis and powertrain and aluminium, in most of its product forms, will play an ever increasing role in all these types of structures.
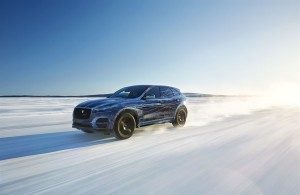
Aluminium lightweighting technology for body-in-white is well established, particularly within Jaguar Land Rover, and more manufacturers will need to switch to aluminium intensive bodies, rather than hang-on parts, to respond to their now urgent and increased need for weight reduction. This must be accompanied by the effective management and recovery of press shop scrap to make the use of aluminium automotive sheet more affordable. The challenge for aluminium extrusions and forgings will be to provide alloys with higher strength without moving to the more expensive aerospace grades of alloy.
Innoval has been providing experience-led technical support to the automotive industry for decades. Read more about how we support aluminium lightweighting projects here.