Posted on: 13th December 2021 by Prof. Geoff Scamans
In this blog Prof. Geoff Scamans tells us about research from the 1980’s which looked at using aluminium as a fuel, and how that theme carries on today.
Aluminium as the fuel of the future
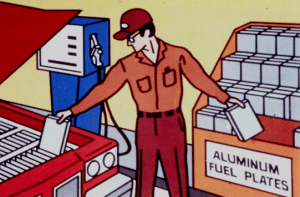
Back in 1986, when I worked for Alcan, I was the co-author of an article published in New Scientist that proposed aluminium as the fuel of the future. It focused on its use in mechanically rechargeable aluminium-air batteries (1).
The carrot dangled was the assumption that if only 1% of cars in the US at the time ran on aluminium as a fuel, then every year this would consume 600,000 tonnes of the metal. This is equivalent to the output of a major primary aluminium smelter. As a result, this was highly attractive to Alcan as a major producer of primary aluminium at the time.
Unfortunately, it turned out to be a false dream even though it was possible to overcome all the major technical hurdles. The practicality of mechanical refuelling and sending the aluminium hydroxide reaction product back to the smelting system was the problem. It could never be energetically or financially favourable compared to a rechargeable battery using green electricity. The best uses for the system were either secret military applications, mainly sub-sea, or reserve power applications for supporting telecommunications.
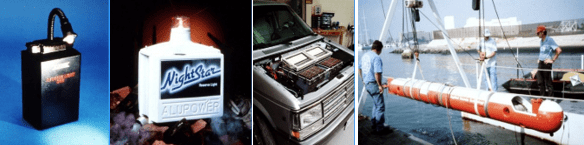
Aluminium-ion battery
A very small component of Alcan’s aluminium-air development programme was a speculative project on aluminium secondary batteries. It was based on the use of an ionic electrolyte, like in the now all-pervasive lithium-ion batteries. Alcan’s Kingston laboratory carried out this work in collaboration and with guidance from Prof. Brian Conway at the University of Ottawa. However, the initial work on secondary aluminium batteries began back in the early 1970s.
This rechargeable system has developed very slowly over the years and is now more popularly known as the aluminium-ion battery. Recently, since 2010, there has been a major surge of interest in this system. Consequently, the pace of research and development of these batteries has increased, and there are several comprehensive review papers (2-5). There is now an array of different systems based either on ionic liquids or polymeric electrolyte systems. The attraction is the significantly increased energy density, power density and fast-charging capability that’s potentially available. This is together with better inherent safety compared to the use of lithium. Furthermore, aluminium is much more abundant and available.
Lithium | Magnesium | Aluminium | Zinc | |
Theoretical Cell Voltage with Oxygen | 3.4 | 3.1 | 2.7 | 1.3 |
Gravimetric Energy Density (Wh/g) | 13 | 6.8 | 8.1 | 1.63 |
Volumetric Energy Density (Wh/cm3) | 7 | 11.8 | 21.8 | 11.6 |
Table 1: The comparative gravimetric and volumetric energy densities of battery anodes.
A recent article describes development work at the University of Queensland (6) which is at the stage of making commercial prototypes. It claims that their latest aluminium-ion technology provides faster-charging batteries with higher power density. They also have a life up to three times greater than lithium-ion. Consequently, the aluminium-ion battery has the potential to displace lithium-ion batteries across the full spectrum of application. However, the developers still have significant technical challenges to overcome.
The need for superpurity aluminium
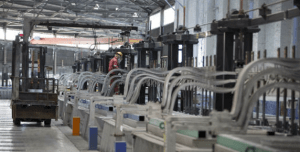
A major hurdle for the primary aluminium-air batteries is the requirement to use aluminium alloys based on superpurity aluminium. The Hoopes Cell electrolytically refines pot-line aluminium from traditional smelters to make this grade of aluminium. Unfortunately, this makes the creation of the battery anode material extremely energy intensive and carbon intensive if green electricity is not used.
Vigeland Metals in Norway makes a significant fraction of the world’s superpurity aluminium. An old Russian-built hydro-electric power station supplies the electricity at extremely low cost. In 2013 Hydro increased their 50% share and acquired full ownership of this metal refinery, and the 180 GWh hydropower station, from Rio Tinto Alcan. The refinery has an annual production capacity of 8,500 tonnes of high-purity (99.99-99.999%) aluminium.
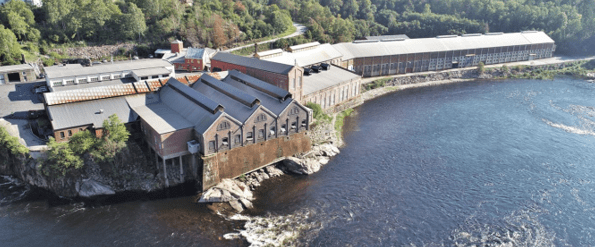
Batteries from scrap?
Interestingly, it is also possible to make pure aluminium from end-of-life aluminium scrap through a similar electrolytic refining process to that used in the Hoopes Cell. In 2011 Alcoa (7) published a technical report on “Membrane Purification Cell Aluminum Recycling”. The aim of the project was to develop an electrorefining molten aluminium process for purifying scrap aluminium to reduce energy consumption and emissions by 75% compared to conventional technology. However, the technology could also produce superpurity aluminium from primary aluminium. Alcoa worked out that the cost of refining using the developed cell was less than the price differential between the cost of the feedstock scrap and the LME primary aluminium price.
It would be rather interesting to see if it’s possible to make aluminium suitable for aluminium-ion batteries using this process from relatively pure grades of scrap. This would be a low carbon and low energy route to providing electropositive plates for these batteries, in keeping with sustainability considerations.
Purification of post-consumer aluminium scrap
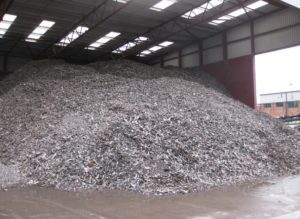
Electrolytic refining of post-consumer aluminium scrap could also be of value for aluminium casting alloys. A potential feedstock could be the mountain of scrap from the eventual reduced demand for internal combustion engines and conventional transmission systems.
The tonnages of aluminium tied up in these secondary alloy-based casting products is relatively large. Refinement of these alloys at the end of life could provide metal for wrought aluminium applications and/or structural casting applications. Furthermore, there could be an opportunity to recover alloying additions like magnesium and silicon from this stream to satisfy alloying requirements.
Alcoa have very recently (8), announced the ASTRAEA technology for purification of any post-consumer aluminium scrap. It can reach a purity level of P0101 (0.01 wt% Si and 0.01% Fe) which is better than the purity of P1020 (0.10% Si and 0.20wt% Fe) aluminium produced in a typical smelter. The intended feedstock for this is Zorba automotive shred. It is quite probable that the membrane purification cell from the 2011 report is the basis of this technology.
Extracting magnesium
In 2016 Adam Gesing, a colleague from the Alcan battery days, and Subodh Das, who has an Alcoan back story, presented an interesting paper. They demonstrated a proof of concept of an electrolytic process for extracting magnesium from recycled secondary aluminium scrap melts (9). It produced a magnesium product suitable as a magnesium alloying hardener additive to primary grade wrought aluminium alloys.
They reported that the process operates at high current efficiency, high magnesium recovery and low energy consumption. Therefore, this could be disruptive and transformational for the magnesium production industry by enabling the recycling of 30,000 tonnes of primary-quality magnesium annually.
So, can we use aluminium as a fuel?
In summary, I don’t think that we should consider aluminium as the fuel of tomorrow or even the future. However, it has a major role to play in rechargeable battery systems, as exemplified by the aluminium-ion battery. Furthermore, other non-aqueous electrolytic processes have a vital role to play for end-of-life aluminium scrap refining and returning secondary aluminium casting alloys to the product cycle. This is also true for the recovery of critical alloying additions like magnesium for alloy formulation. Thankfully, all of these help to replace the need for primary production.
References
1. Nigel Fitzpatrick and Geoff Scamans, Aluminium is a fuel for tomorrow, New Scientist 17 July 1986 pp34-39
2. Meng-Chang Lin, Ming Gong, Bingan Lu, Yingpeng Wu, Di-Yan Wang, Mingyun Guan, Michael Angell, Changxin Chen, Jiang Yang, Bing-Joe Hwang and Hongjie Dai, An ultrafast rechargeable aluminium-ion battery, Nature volume 520, pages324–328 (2015)
3. Tilmann Leisegang, Falk Meutzner, Matthias Zschornak, Wolfram Münchgesang, Robert Schmid, Tina Nestler, Roman A. Eremin, Artem A. Kabanov, Vladislav A. Blatov and Dirk C. Meyer,The Aluminum-Ion Battery: A Sustainable and Seminal Concept?, Front. Chem., 01 May 2019, https://doi.org/10.3389/fchem.2019.00268
4. Du Yuan, Jin Zhao, William Manalastas Jr., Sonal Kumar and Madhavi Srinivasan, Emerging rechargeable aqueous aluminum ion battery: Status, challenges and outlooks, Nano Materials Science, Volume 2, Issue 3, September 2020, Pages 248-263, https://doi.org/10.1016/j.nanoms.2019.11.001
5. Xuejing Shen, Tao Sun, Lei Yang, Alexey Krasnoslobodtsev, Renat Sabirianov, Michael Sealy, Wai-Ning Mei, Zhanjun Wu and Li Tan, Ultra-fast charging in aluminum-ion batteries: electric double layers on active anode, Nature Communications volume 12, Article number: 820 (2021), https://doi.org/10.1038/s41467-021-21108-4
6. UQ technology powers up greener alternative to lithium ion in Brisbane manufacturing deal, Australian Institute for Bioengineering and Nanotechnology, 23 April 2021, https://www.uq.edu.au/news/article/2021/04/uq-technology-powers-greener-alternative-lithium-ion-brisbane-manufacturing-deal
7. David H. DeYoung, Cong Wang and James Wiswall, Alcoa Final Technical Report, Membrane purification cell for aluminium recycling, DOE Award Number: DE-EE0003466, November 2011
8. Alcoa Announces Technology Roadmap to Support Its Vision to Reinvent the Aluminum Industry for a Sustainable Future, November 8, 2021 https://investors.alcoa.com/news-releases/news-release-details/2021/Alcoa-Announces-Technology-Roadmap-to-Support-Its-Vision-to-Reinvent-the-Aluminum-Industry-for-a-Sustainable-Future/default.aspx
9. Adam J.Gesing, Subodh K. Das and Raouf O.Loutfy, Production of magnesium and aluminium-magnesium alloys from recycled secondary aluminium scrap melts, REWAS 2016: Towards Materials Resource Sustainability, TMS (The Minerals, Metals & Materials Society), 2016
Foundry alloys image credit: Norsk Hydro ASA