Posted on: 5th May 2016 by Vicente Martin
Aluminium foil is a key material for the packaging industries. It is ubiquitous in many packaged product forms, such as milk or juice cartons and the blister packs dispensing pharmaceutical tablets. No competing material has been able to match its combination of formability, printability and excellent barrier properties, making aluminium foil unsurpassed when it comes to protecting and preserving our complex food supply chains.
Even though aluminium foil has been manufactured for well over a century, the production of top quality foil for converting applications still has elements that are not universally understood or which are without a clear, common scientific understanding. Manufacturers rely on maintaining the stability of processes developed through trial and error long ago. However, small changes in the supply chain or process can cause defects that are difficult to troubleshoot.
Final annealing of thin foil is an example of a poorly understood process with a large number of different factors that can interact to produce good or bad results. It is one of the most critical operations in foil manufacturing with a direct impact on customer performance. It’s also a limiting factor in the availability of wider foils.
After annealing, there is a fine balance between incomplete degreasing which leads to adhesion problems during the conversion process, and poor unwinding quality which causes tears or holes in the material when unwound by an end user. Both instances result in coils being returned to the supplier.
About the aluminium foil coil
To appreciate the critical nature of the final annealing stage, we first need to understand a little about the coil and what happens to residual rolling oil during the annealing process.
A coil of 6-micron thick converter foil is far from being solid; there is a gap between layers of less than 1 µm, which makes the effective density of the coil lower than the aluminium.
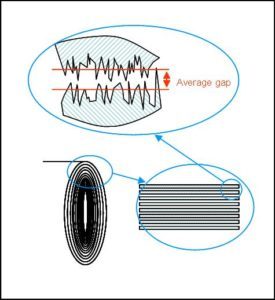
Right after coiling this gap will be mainly filled with residual oil from the mill. After annealing it should be filled mainly with air. In the process of the final anneal, oil needs to vaporise and flow through the width of the coil to the edges through this small gap. This distance is up to 800 mm from the centre of the coil to the edge of the coil. The physics of the oil diffusion through these gaps is a long way from normal fluid dynamics, and the pathway resembles more a porous structure than a tunnel. Because the metal roughness is of the same order of magnitude as the gap, this convolutes the path the oil has to percolate through (Figure 1).
The air gap between laps, the coil geometry, oil characteristics, temperatures and vapour pressure exert a strong influence on oil removal. Additionally, the chemistry of the oils and the additives used during the rolling of aluminium foil products means the dynamics and energies relating to the adsorption to the surfaces need to be considered fully.
Factors affecting annealing performance
Batch annealing is recognised as a crude, imperfect non-homogeneous process. To date, alternative chemical or plasma cleaning techniques haven’t been able to provide a workable, cost-effective in-line solution to remove the residual rolling oil in thin foil.
The factors affecting annealing performance span the entire rolling process:
- Rolling mills always leave some residual oil on the surface that will need to be removed. Bespoke containment systems try to keep this residual oil to a minimum and homogenously distributed, but unless an oil free rolling technique is developed, it will always be a problem. Oil chemistry and heavy oil contamination play a key role in determining oil evaporation kinetics so usually the chemistry and maintenance monitoring system is key to quality. Understanding the life cycle of the oil through contamination, recycling systems and filtration will allow monitoring to be optimised. Mill maintenance and flatness control will also be instrumental in keeping problems to a minimum.
- Separators will directly affect coiling density and the geometry of the long, thin path the oil needs to follow to exit the coil. A balance between a stable coil without telescope and a wide interlap space needs to be found in a process involving dimensions of a fraction of a micrometre.
- Foil annealing times are often the longest in the whole of the aluminium industry with some practices lasting up to a week. Temperature cycles, atmospheric control and purging need to be tuned with the kinetics of lubricant species removal to provide a perfect surface for conversion, while at the same time minimising detrimental changes to the foil oxide layer.
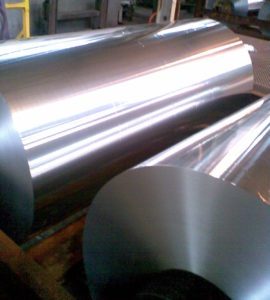
Frequently, problems arise even in the best controlled operation. In these cases surface chemistry techniques (Surface carbon, GC, TGA, FTIR, etc.) and experienced trouble-shooters are invaluable to detect and identify the origins of the problems. The correct mix of plant data analysis, field measurements and laboratory analytical measurements combine to pinpoint weak points in the process and identify the likely origin of defects.
Innoval’s foil experts have a huge amount of process troubleshooting experience and they can help you with faster resolution of incidents and elimination of endemic quality problems.
You can read how our expertise was put to good use at Xiashun Aluminium Foil Co., Ltd in China here.
We also offer a training course about aluminium foil packaging.